Table of Contents
Principles of Cleanroom HVAC Balancing and Calibration
This post answers the question, how do I calibrate airflow for an ISO 7 medical device cleanroom? Before cleanroom validation, a cleanroom requires mechanical calibration and balancing. HVAC calibration ensures that the room meets the performance standards for differential pressure, air change rates, and uniform airflow distribution.
Medical Device Cleanroom Build Guide
Part 1: Walls, Windows, & Containment
Part 2: Electrical, Mechanical & Partitions
Part 3: Fan Filter Units – Ceiling Grids
Part 4: VCT Cleanroom Flooring
Part 5: HVAC Design & Fan Filter Integration
Part 6: Pressure Differentials, Humidity and Temperature Calibration
Part 7: Cleanroom ISO Class Validation
The Building Blocks of a Cleanroom HVAC System
There are a few basic cleanroom control principles that determine the efficacy of a controlled environment and its cleanliness rating. Testing and validation remain important for any HVAC system regardless of its critical or general use. Energy, airflow, cleanliness, and even acoustics are important metrics for the end-user.
Contrasting Residential vs Cleanroom HVAC Systems
Residential and single-story HVAC systems have rather rudimentary control methods. A thermostat regulates the on/off cycles of the heater and blower to maintain a relatively consistent temperature profile. This makes for a rather efficient system with a self-automating operation.
In a residential environment, supply and return air maintain neutral pressure. The difference in room pressure between one room to the next is essentially unnoticeable. This is approximately the point where the similarities between standard HVAC systems and high-performance cleanroom suites end.
In a residential environment, supply and return air maintain neutral pressure. The difference in room pressure between one room to the next is essentially unnoticeable. This is approximately the point where the similarities between standard HVAC systems and high-performance cleanroom suites end.
Before we consider the operating system as a whole, let’s take a moment to consider it’s air induction system.
Contrasting Cleanroom HVAC Duct Systems and Designs
The complete science of a cleanroom HVAC is not the focus here, however, CED Engineering provides a great guide on fundamental HVAC calculations, best practices, and performance expectations for commercial HVAC design.
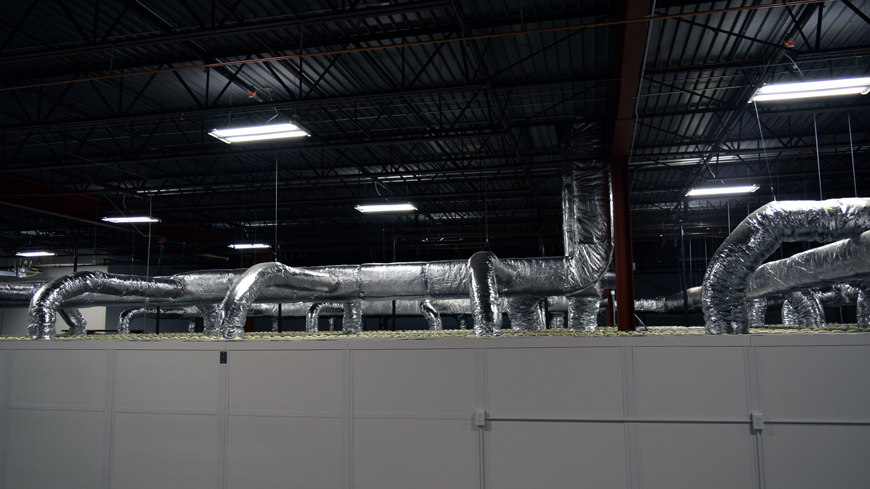
Cleanroom Duct Configuration
The above image shows a modular HVAC design that combines elements from two methodologies “spider configuration” and “reduced plenum” HVAC design systems (Pg. 43). Small branches connect the supply trunks to Independently sealed plenums which serve air to the T-grid equipped ceilings and fan filter units for induction.
The ISO 7 space of this cleanroom (primary production area) requires more airflow than the ISO 8 space, thus designers evaluate the airflow requirements of each cleanroom zone and calculate min/max input requirements based on room size and air change requirements. Some cleanroom designs use solid ducting, however flexible ducting has advantages for a modular configuration.
Flexible Duct Advantages
A flexible system provides far more versatility than rigid ducts, especially when regarding modular cleanrooms. A lighter material reduces install time and dedicated hardware requirements. The system is more flexible to existing structures and doesn’t require an extraordinary amount of effort for extensions, demolition, or later modifications such as adding more square footage or additional cleanroom suites.
Proper fabrication and installation technique is a standard, but not always a given. Metal on metal ducts require project-specific engineering, sometimes leading to insufficient room or fittings squeezed into tighter spaces (pg. 47).
The gentle curvature of a flex duct prevents air pressure drop and turbulence with far fewer preliminary decisions, such as designating alternatives when a hard ducted radius elbow cannot fit or when navigating existing HVAC systems. Notwithstanding, improperly installed or engineered cleanroom flex ducts will also incur performance losses.
Related: PAC’s Cleanroom HVAC & Air Filtration Knowledgebase >>
Cleanroom Plenum Design
Each “leg” delivers air from a ceiling inlet to an interstitial space within the ceiling called the plenum. The plenum feeds multiple fan filters with clean, fresh air in a pass-through cleanroom or makeup air in a recirculating cleanroom.
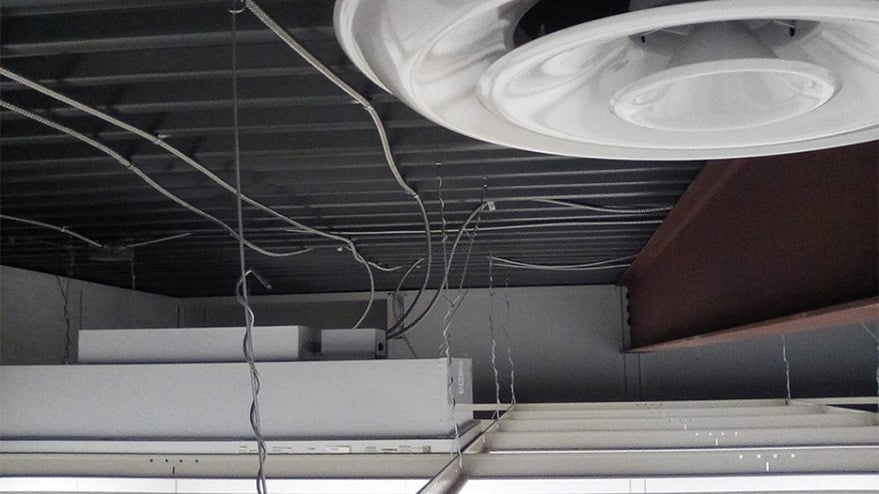
The picture above shows the ceiling assembly with just lights and fan filter units installed. Before startup, all of the wiring, fire suppression, air hoses, and CAT5 lines require integration into the plenum space.
HEPA fan filter units with an inline prefilter force air from the plenum into the cleanroom. Air enters the cleanroom and passively exhausts through wall chases.
The exiting air is either reintroduced into the handling system for filtration (recirculating cleanroom) or exhausted to an external area (single-pass cleanroom) to a parallel space within the building.
Cleanroom Wall Chases and Air Exhaust
A wall chase is an empty wall cavity that exfiltrates dirty air. The design functions passively, in that the higher-pressure in the cleanroom entices air outward through the chases with minimal turbulence.

Because the air contains no contaminants or hazardous compounds, exhausting the air to an uncontrolled space outside of the cleanroom improves air quality as a whole throughout the facility.
Cleanroom Construction Part 3 | Fan Filter Unit Assemblies
Cleanroom Startup Considerations
Now that we’ve covered the basic delivery and handling of air to the cleanroom, let’s consider some questions we’ll need to answer after initial cleanroom startup:
- Is each fan filter unit receiving enough airflow to prevent starving scenarios?
- Is each fan filter unit receiving enough power to achieve minimum operating speed?
- Is each fan filter meeting its expected CFM delivery?
- Is each fan filter responding to controls from the central or remote control system?
Cleanroom shutdown for even 20 minutes is enough time to drop an entire tier on the ISO classification scale.
Advantages of a Cleanroom Fan Filter Control System
The benefit of a CleanPro® cleanroom control system is realized with handy features like an alarm if the room were to lose pressure. A room that gains or loses pressure differential rapidly may indicate a serious issue. A slow increase or decline most likely signals filter load or leaks that require filter maintenance or replacement.
Automated fan speed control significantly increases the life of both fan filters and their blower motors. The calendar-based programming of each individual fan filter’s RPM by either macro zone/group control allows shutting down a specific part of the cleanroom without full pressure loss. Automation, power savings, and off-site monitoring are core advantages of a digitally-driven fan filter control system, but also another big advantage during the most basic maintenance and troubleshooting tasks.
CleanPro® Monitoring Solutions are SMART enabled systems for remote cleanroom management and alarm monitoring. You’ll find these ISO-9001/2008 certified systems in over 200 hospitals, clinics, laboratories, and medical device manufacturing operations throughout the world.
FAQ: What is the Recommended Air Change Rate for a Medical Device Cleanroom?
HEPA filtered air supply is a cornerstone of any cleanroom. When projecting the final cleanliness of room air, the number of air changes per hour (ACPH) is one of the most indicative cleanliness values for non-unidirectional cleanroom designs.
Air change rate (ACR) is the total air volume added and removed from a space over a given period of time. Standard living spaces are designed around 4 air changes per hour. This an ISO 7 / ISO 8 medical device cleanroom is specified for 55 air changes per hour.
Read More: How do I Calculate Air Changes Per Hour?
Need Help with a Modular Build?
Custom-specified modular components provide design freedom for everything you need and cost savings for everything you don’t. Modular hardware and prefabricated panels reduce material and labor during onsite installation and lead cost savings. The entire containment structure is assembled with just a small team, minimal tooling, and little on-site modification or heavy equipment.
PAC (that’s us) internally coordinates cleanroom installation services, cleanroom design, and contamination control outfitting. Our turnkey customers often opt for end-to-end outfitting because we have both expertise and supply chain services for bulk shipments of general and critical cleanroom supplies.
Because we specify and source the entire build down to every component, we’re intimately familiar with every detail. That’s the only way we can guarantee that every PAC cleanroom build meets final ISO validation and organizational goals.
PAC cleanroom specialists provide engineering, construction, outfitting, and environmental solutions for casual and critical production environments.
We’ve developed a culture of specialists that assess your needs and solve your manufacturing problems. Solving the right problem starts with asking the right expert. How can we help?
Related Posts
-
Medical Device Cleanroom Construction Part 1: Walls and Installation
How is a medical device cleanroom built? Here's a component-by-component guide to ISO Class 7 cleanroom construction.
-
Medical Device Cleanroom Construction Part 2: Doors, Electrical, and Layout
In medical device cleanrooms, a common configuration is an ISO 8 gowning room and ISO 7 primary production area. A cascading air flow design and positive pressure HVAC calibration move the cleanest air at the…
-
Medical Device Cleanroom Construction Part 3: Fan Filter Units - Ceiling Grids
In this post, we overview technical considerations for clean room fan filter unit selection, installation, and features. You'll learn how PAC approaches design and configuration of cleanroom HEPA filter units and fan filter housing specifications.…
-
Medical Device Cleanroom Construction Part 4 - VCT Flooring Design
There are a few final preparations required before the final cleanroom flooring installation. Here's what to expect and consider for cleanroom tile installations and flooring installation.
-
Medical Device Cleanroom Construction Part 5: HVAC Balancing & Calibration
Before cleanroom validation, a cleanroom requires mechanical calibration. HVAC calibration first ensures that the room meets the performance parameters which would deliver the expected results during final ISO validation, such as differential pressure, air change…
-
Medical Device Cleanroom Construction Part 6: Pressure Differentials, Humidity and Temperature Calibration
The central controller integrates the data from both the thermostats, fan filter processors, and room-side environmental sensors. Fan filter speed is then adjust by each group to achieve the specified room pressure while at ideal…
-
USP 800 Cleanroom Construction Hazardous Compounding: Options and Alternatives
There are a few options available to cleanroom facilities who require new upgrades for USP 800 compliance. The best option will depend on the variables of the facility and cleanroom in question. Option A: Convert…
-
Cleanroom Fan Filter Testing and Maintenance - HEPA Filter Replacement and Troubleshooting
How do I know when to replace my cleanroom HEPA air filters? How do I test a cleanroom HEPA filter? What are the best practices for cleanroom HEPA filter replacement?
-
Medical Device Cleanroom Classification
What Kind of Cleanroom Do I Need for a Class II Medical Device? What About Class III? This post classifies medical device cleanrooms for manufacturing and packaging.