There are a few options available to cleanroom facilities who require new upgrades for USP 800 compliance. The best option will depend on the variables of the facility and cleanroom in question.
Option A: Convert an existing clean area into a negative pressure compounding room and storage area
Option B: Build a new structure specifically for the handling of hazardous drugs
Option C: If handling Category 1 CSPs, build a non-classified structure with the appropriate BSII+ containment system.
The First Step
The most helpful step for successfully building or retrofitting a USP cleanroom is contacting your State Board of Pharmacy. Each state has unique requirements for USP 800 compliance. The content below is considered educational and does not constitute a recommendation for your cleanroom.
Modifying Cleanrooms for USP 800 Compliance
Most of the inquiries we receive on USP 800 cleanrooms require retrofitting of an existing structure or cleanroom. However, the exact modifications vary. Space is usually one of the most limiting factors.
Sometimes, cleanrooms with adequate storage space, buffer zones, and external ventilation may simply require a reverse fan filter unit, epoxy paint, a USP qualified door, and water channel gauge.
In other cases, PAC works directly with the manufacturer to customize new hardware for retrofitting new hardwall structures to existing hard wall structures panels to existing structures.
If you think to modifying your existing cleanroom is the right choice for you, the PAC cleanroom network covers most of the US, Mexico, the Caribbean, and Central America.
USP 800 HVAC Considerations
A Magnehelic gauge is a pressure differential monitoring instrument integrated into a shared wall with rooms of different pressure on either side. An experienced local contractor, facilities engineer, or HVAC installer is usually capable of managing the project.
USP 800 requires an externally vented exhaust. Air that would normally be recirculated into the air handling system is less available: the system must accommodate greater volumes of make-up air, and thus also provide the extra capacity for heating and air conditioning. Not providing enough air to the cleanroom may trip shut down alarms, create a differential that is too negative, or cause failures and burn out within fan drives.
In most cases, the small footprint of a hazardous compounding room provides sufficient make up air. In contrast, our dedicated USP 800 solutions provide independent air handling and ducting if necessary, usually via a cleanroom mounted or roof-mounted air handling source.
Advantages of Variable Drive Fans for USP 800 Cleanrooms
The suite will require rebalancing to validate adequate pressure differentials. Upgrading your fan filter system to remote variable drive controllers is an efficient way to balance differential pressure. A variable drive fan filter system allows balancing of initial pressure calibration, but also is also a robust system when overcoming filter load throughout the life of the HEPA filter.
Dynamic fan speed controllers reduce overall fan filter maintenance costs. Static drive fan filter units will require more frequent HEPA filter replacement because fan is speed is not adjustable to overcome filter blockage.
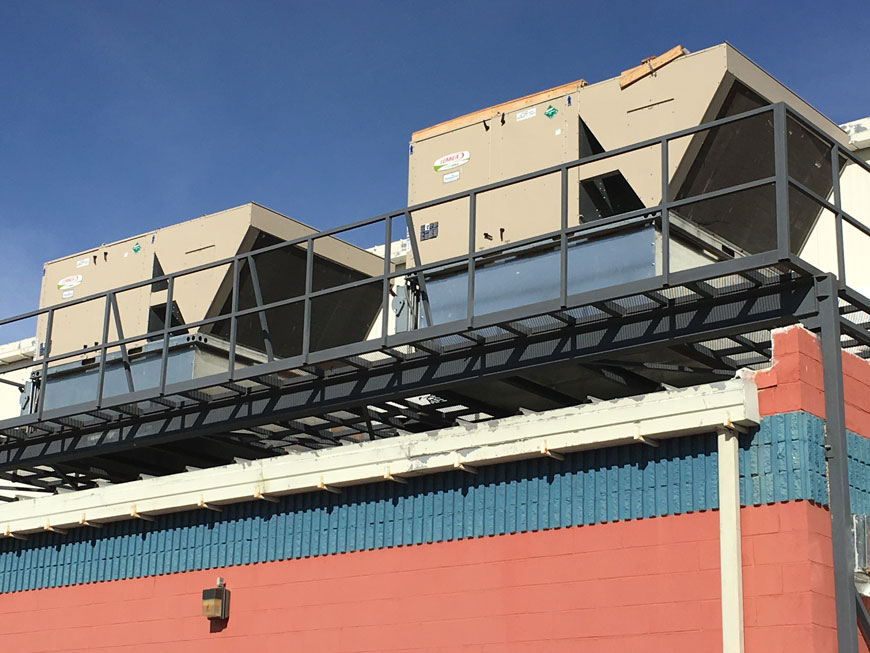
What if an HVAC system upgrade is not feasible?
“Where upgrades to the current air conditioning system are not an option, an alternative would be to reposition the fan filter units that outfit the C-PEC, C-SEC and negative pressure storage room six to eight inches below the air registers that supply air to these spaces. This will allow the fan filter units to supplement air intake with the surrounding ambient air rather than pulling exclusively from the facility’s system. This alternative can provide enough air supply to meet USP <800>’s air change per hour and ISO air standards while allowing the fan filter equipment to operate efficiently.” – Simplex Engineering – PAC Cleanroom Construction Network Allies
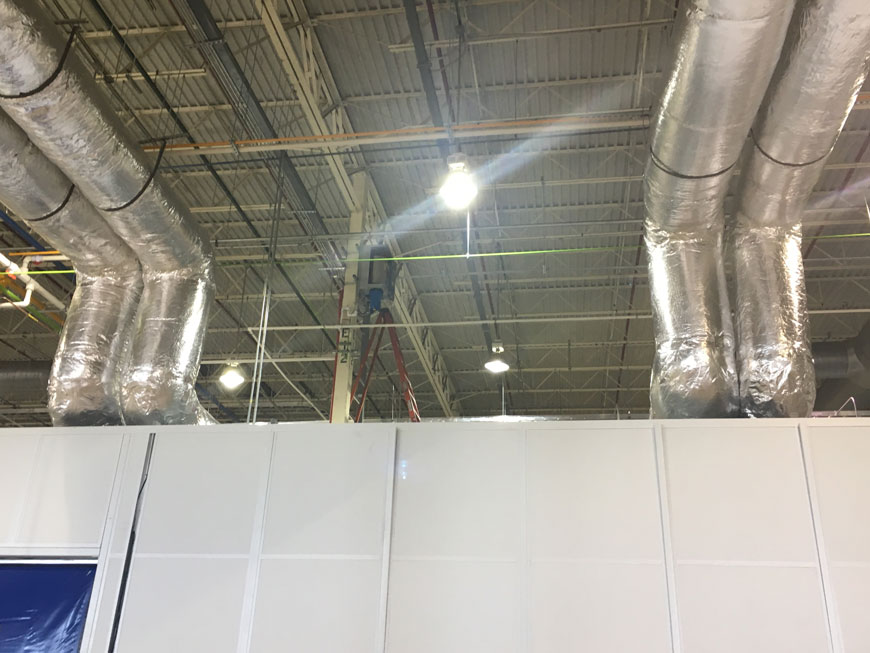
What if the current cleanroom pressure is too negative?
Some facilities face the problem of cleanroom pressure being too negative. USP 797 required negative pressure for HDs of at least 0.01 inch water channel, but did not specify limitations.
USP 800 designates a zone only acceptable between 0.01 and 0.03 in WC. Excessive negative pressure increases the risk that gaps, cracks, conduits, and entrances pass contamination inward to critical areas.
An over-built system is more taxing on the air handling system, thus less efficient and more costly. In the case of an existing cleanroom, consulting the original cleanroom contractor or manufacturers is the best way to vette alternative options.
USP 797 and USP 800 Construction
For a full USP compounding suite including both 797 and 800 containment, some may think this requires independently constructed partitions, multiple gowning rooms, air showers, and individual entry and exit. PAC’s USP 797 and 800 cleanrooms provide cross-functional structures with parallel rooms that share entrances and gowning spaces.
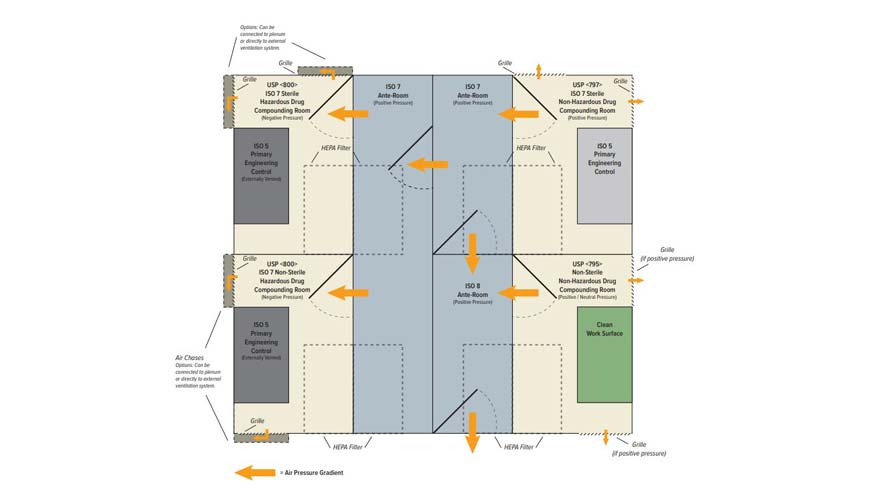
Parallel designs provide the proper ante-room requirements via cascading air systems. For example, the ISO 8 ante-room meets the requirements for a USP 795 area, which also provides access to the more critical gowning for the USP 797 and 800 rooms. Integrated designs reduce the overall footprint, structural demands, and air requirements for each suite.
View All USP Cleanroom Configuration Options
How Much Do USP 800 Upgrades Cost?
The cost of retrofitting a room among a jungle of preexisting HVAC, plumbing, and electrical systems is hands-on, disruptive, and may quickly exceed the cost of a new build. Normally the cost of a new cleanroom build is quoted on a square foot basis, usually somewhere between $100 – $300 per sq. ft. However, this pricing does not apply in the case of a retrofit.
Alternatives to Modifying an Existing Cleanroom
Replacing an existing structure with a prefabricated cleanroom is sensible if the room were to otherwise require relocation, unreasonable downtime, or exhaustive upgrades. Modifying a stick-built cleanroom is hands-on, particularly for internal facility staff, who essentially serve as the construction manager and direct point of contact for the general contractor/foreman. This often requires facilitating building permits and scheduling non-cleanroom engagements such as flooring, plumbing, and electrical.
Is A Cleanroom Rebuild Worth Considering?
Prefabricated cleanroom installation is non-invasive, has fewer construction requirements, and only requires a small team for installation of walls, windows, doors, passthroughs, ect. The systems are self-supporting and if required, capable of bearing roof-mounted office spaces, mezzanines, generators, and air handling units.
Our pharmaceutical-grade hardwall cleanroom systems ship palletized, with everything pre-engineered and pre-cut at the factory after delivery of finalized blueprints. For USP rooms, a small team can often install the structure in a single day (and still beat rush hour traffic). PAC manages pre-engineering, scheduling, delivery, design iterations, any component alterations, and sometimes construction.
What is the Solution?
PAC does provide a la carte solutions for USP 800 retrofits (Get construction help). In most cases, the final installation and validation are handled by the customer. The configuration and costs are determined by a few different factors such as the size of the space, electrical/HVAC integration, the number of walls required, and prefabrication requirements for affixing the structure — and finally — ensuring flush fits of doors, windows, and air seals. The room is then calibrated to ensure the correct negative pressure differential and airflow which includes a dedicated monitoring gauge.
It’s beneficial to understand your specific requirements based on your state regulatory inspectors. We can help you determine these requirements, notwithstanding we do bill these costs in addition to the above costs of components, hardware, filtration, wall systems, doors, ect.
The only way we can guarantee a cleanroom build meets your final validation requirements is by intimately understanding all construction variables and design components. While we can provide you an assessment at no cost, or provide end-to-end supply of passthroughs, doors, filter media, fan filter units, ect, modifying an existing cleanroom has many variables and is subject to interpretation by your local inspector.
It’s usually worth consulting with your local Board of Pharmacy authority before providing specifications or requesting a quote.
Need Help on a USP 800 Build?
Because we’re not limited to any one manufacturer, installer, or construction/component solution, our access to factory direct pricing is usually more competitive, if not better than any general contractor.
A turn-key modular system is often a choice selection when new facilities struggle to identify an internal lead for the project, or lack internal expertise on cleanroom environments.
The PAC cleanroom network includes solutions in nearly every mainland territory of the United States. That also includes number regions in Mexico, Central America, the Caribbean, Puerto Rico, Costa Rica, and the Dominican Republic. A second opinion and consultation are always free.
Our cleanroom components and turn-key solutions are best-in-class. Because we can provide both turnkey cleanrooms and all of the necessary cleanroom components a la carte — such as doors, passthroughs, and furniture. For help with a cleanroom construction project, call during business hours or answer a few short questions and we’ll get back to you within 24 – 48 hours.
Ask Our Engineers
Ask A Cleanroom Expert
Get a Free QuoteExplore Cleanroom Designs
Read About USP Cleanroom Design
USP CleanroomsUSP 800 Compliance Overview
USP 800 Overview & Solutions
Find SolutionsDisclaimer
Consulting a cleanroom specialist would be in any healthcare institution’s best interest and can help alleviate many of the challenges associated with compliance. In addition to detecting the potential space or building infrastructure modifications needed, a cleanroom specialist can help to identify which approach—modular or stick-built construction—is the best fit. Factors such as budget, work flow and anticipated future growth will be taken into consideration and accounted for.
It is recommended for healthcare administrators and employees involved in the hazardous drug process to read USP <800> in its entirety and understand all requirements and recommendations set forth by the chapter. Though USP <800> will impact many healthcare institutions, it is undisputed that the guidelines set forth by the chapter for the handling of hazardous drugs are an important step for protecting healthcare workers and the environment moving forward.
Compliance requires temporal evaluation on a case-by-case basis according to state and federal law. It is the responsibility of the manufacturer to outline, define, revise, and validate standard procedures and protocols internally.
Web content provided by Production Automation Corporation (PAC) makes no claims as to the final interpretations or implementation of regulatory documents provided by the FDA, State Board of Pharmacy, or United States Pharmacopeia (USP).
Related Posts
-
USP <800> Compounding Cleanrooms
Updated: USP 800 is a cleanroom standard issued in March of 2014 by the United States Pharmacopeial Convention (USP). The deadline December 2019 for compliance may change.
-
Upgrading a USP 797 Cleanroom to USP 800?
New USP guidelines may present challenges for compounding facilities. Some facilities need infrastructural and mechanical modifications for compliance. System evaluation includes duct systems, HEPA fan filters, differential pressure standards, air monitoring, and external air exhaust…
-
How Does USP 800 Change Storage and Unpacking of Hazardous Drugs?
Facilities unpacking hazardous drugs within a negative pressure room do not require procedural changes to meet USP unpacking area requirements. Facilities unpacking HDs within positive pressure ante rooms or facility spaces will require reconsideration.
-
Updated: USP Sterile Compounding 2019
First published in 2004, USP Chapter has undergone proposed revisions as of July 2018. These revisions are now available for public comment.
-
USP <800> Compounding Cleanrooms
Updated: USP 800 is a cleanroom standard issued in March of 2014 by the United States Pharmacopeial Convention (USP). The deadline December 2019 for compliance may change.