Precision is of utmost importance in the complex field of semiconductor equipment manufacturing and achieving perfection starts by establishing a controlled environment. At PAC, we recognize cleanrooms are not merely enclosed spaces; they are meticulously engineered ecosystems designed to safeguard the integrity of manufacturing processes. Our recent ISO Class 6 cleanroom collaboration with a well-established semiconductor client showed our seamless management of the entire cleanroom process, emphasizing our commitment to excellence.
Project Breakdown: Elevating Precision in Semiconductor Cleanroom Expansion
With a proven track record of successful cleanroom constructions, PAC earned the trust of a semiconductor client based in Phoenix, Arizona, who selected us to spearhead their expansion project. Taking charge from conceptual design to flawless execution, PAC seamlessly navigated the intricacies of the project, ultimately delivering exceptional results.
Planning and Design: Crafting Precision from Blueprint to Reality
In cleanroom construction, the initial stages are pivotal. Meticulous planning and thoughtful design lay the foundation for an environment where precision reigns supreme. From the outset, PAC exemplifies its commitment to excellence by closely collaborating with our customers and suppliers to understand their unique requirements and challenges.
Several critical factors demand thoughtful consideration for cleanroom design for semiconductor manufacturing. The semiconductor industry operates at the cutting edge of technology, where even the tiniest particle can disrupt the delicate processes involved in manufacturing advanced semiconductor devices. As such, the cleanroom must be designed to achieve and maintain the highest cleanliness levels and purity standards.
The Crucial Alliance Between ISO Standards and Particle Control
Cleanroom design adheres to ISO standards, with ISO 14644-1 being a cornerstone in establishing and maintaining the cleanliness of the environment. This international standard specifies the maximum allowable particle counts in the cleanroom air, categorizing cleanrooms into different classes based on their cleanliness levels. Adhering to ISO standards ensures a regulated approach, offering a clear benchmark for particle control and minimizing the risk of contamination.
Nanoscale precision is the standard in the semiconductor industry and compliance with ISO guidelines is non-negotiable. Stringent control over airborne particles is essential to guarantee the reliability and performance of semiconductor devices. PAC’s cleanroom designs align with these standards, providing our clients with the assurance that their manufacturing processes are conducted in an environment where particle contamination is virtually eliminated.
ISO 14644-1 Cleanroom Standards | |||||||
---|---|---|---|---|---|---|---|
Classification | Maximum Particles/m3 | FED STD 209E Equivalent | |||||
≥0.1µm | ≥0.2µm | ≥0.3µm | ≥0.5µm | ≥1µm | ≥5µm | ||
ISO 1 | 10 | 2.37 | 1.02 | 0.35 | 0.083 | 0.0029 | |
ISO 2 | 100 | 23.7 | 10.2 | 3.5 | 0.83 | 0.029 | |
ISO 3 | 1,000 | 237 | 102 | 35 | 8.3 | 0.029 | Class 1 |
ISO 4 | 10,000 | 2,370 | 1,020 | 352 | 83 | 2.9 | Class 10 |
ISO 5 | 100,000 | 23,700 | 10,200 | 3,520 | 832 | 29 | Class 100 |
ISO 6 | 1.0 x 106 | 237,000 | 102,000 | 35,200 | 8,320 | 293 | Class 1,000 |
ISO 7 | 1.0 x 107 | 2.37 x 106 | 1,020,000 | 352,000 | 83,200 | 2,930 | Class 10,000 |
ISO 8 | 1.0 x 108 | 2.37 x 107 | 1.02 x 107 | 3,520,000 | 832,000 | 29,300 | Class 100,000 |
ISO 9 | 1.0 x 109 | 2.37 x 108 | 1.02 x 108 | 35,200,000 | 8,320,000 | 293,000 | Room Air |
Semiconductor Processes: Shaping Layout and Component Choices
The layout and component choices in cleanroom construction are intricately linked to the specific semiconductor processes that will be carried out within. Different processes require varying levels of cleanliness, temperature control, and isolation.
The cleanroom layout must facilitate a smooth flow of processes, preventing cross-contamination and ensuring optimal efficiency. Component choices, from flooring to wall surfaces, are selected to minimize particle generation, electrostatic discharge, and chemical emissions.
Key Construction Phases
The success of any cleanroom project hinges on seamless coordination and execution across key construction phases. PAC orchestrated this project, starting from precise planning and design, transitioning to construction, and culminating in validation. Our core responsibility encompassed coordinating cleanroom resources, ensuring the client’s vision seamlessly translated into a functional and compliant cleanroom.
Cleanroom Walls: Precision in Every Panel
PAC’s commitment to precision is clear in the choice of cleanroom wall and ceiling systems. Our team of experts chose a furring wall design for this cleanroom, considering that it was constructed in a pre-existing environment. A furring wall is typically made of lightweight materials and is constructed parallel to the room’s existing wall, creating an air gap. This gap allows for the circulation of filtered air and aids in preventing the infiltration of contaminants in the cleanroom.
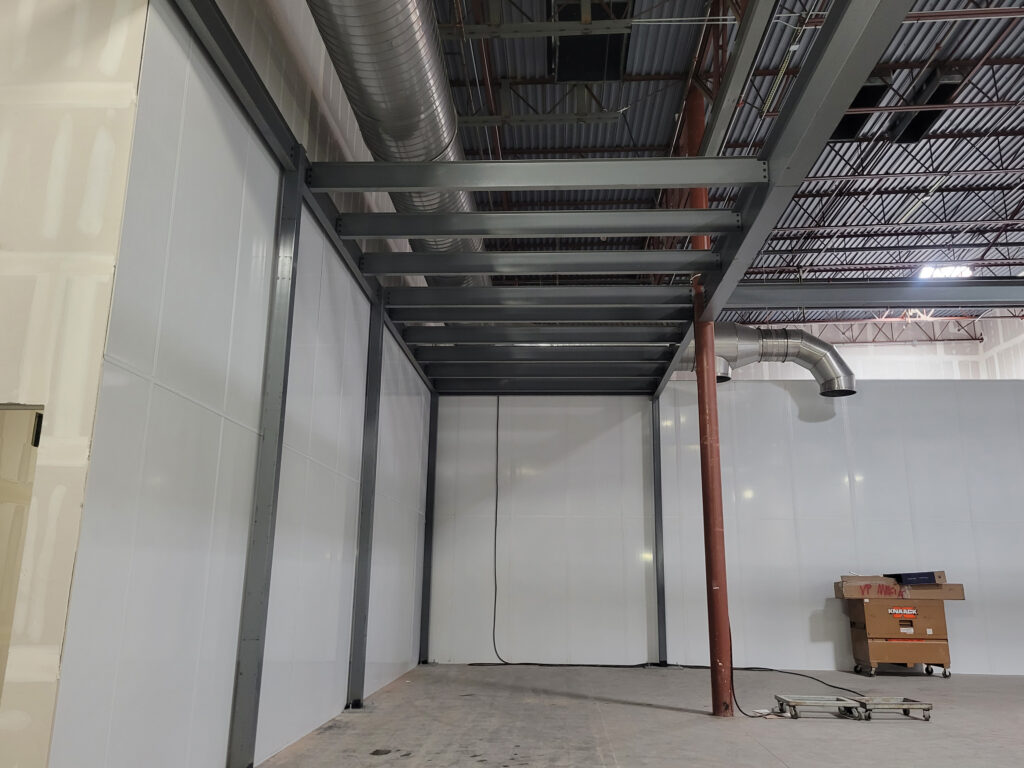
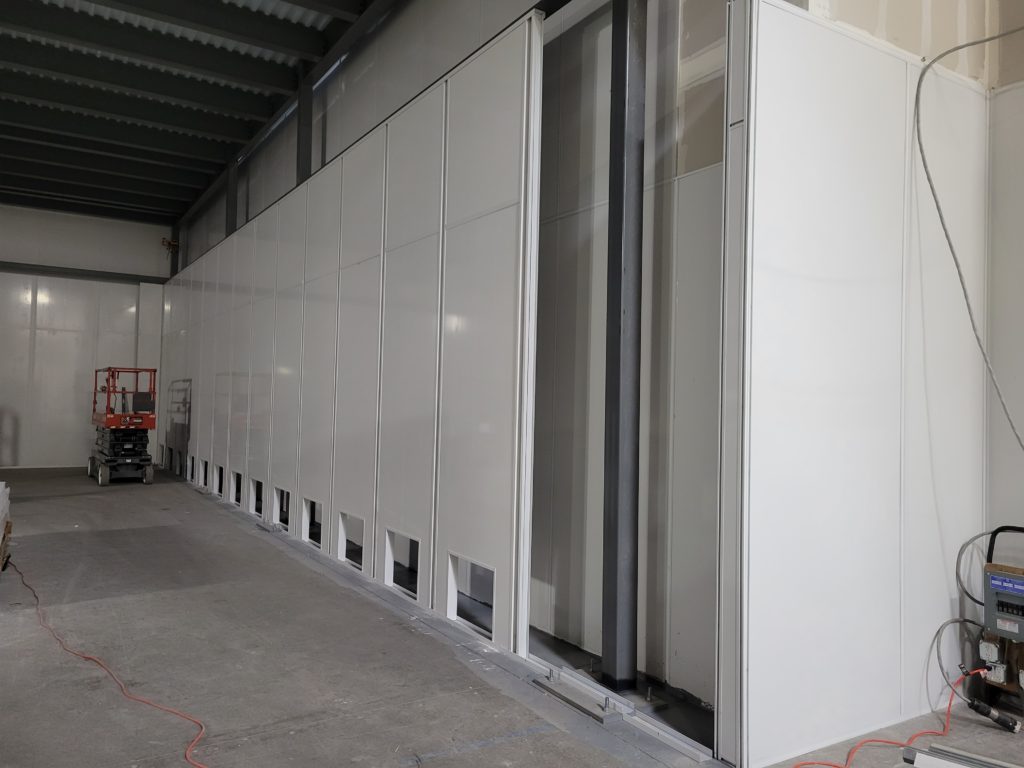
Cleanroom Ceiling System
Above the ceiling for this project, we installed a system of ceiling walkways that would provide a safe and efficient way to change out the cleanroom’s fan filters and lights. A walkable ceiling system grants direct access to critical utilities and filtration systems, minimizing disruptions and downtime during equipment maintenance and filter replacements. These systems also offer an added benefit to the construction process by allowing for simultaneous work to be done above and below the ceiling.
The selected systems offer a blend of functionality and efficiency, providing a controlled environment that aligns with ISO Class 6 standards. These systems contribute to the stringent particle control necessary for semiconductor manufacturing, ensuring that the cleanroom remains a pristine space where technology unfolds.
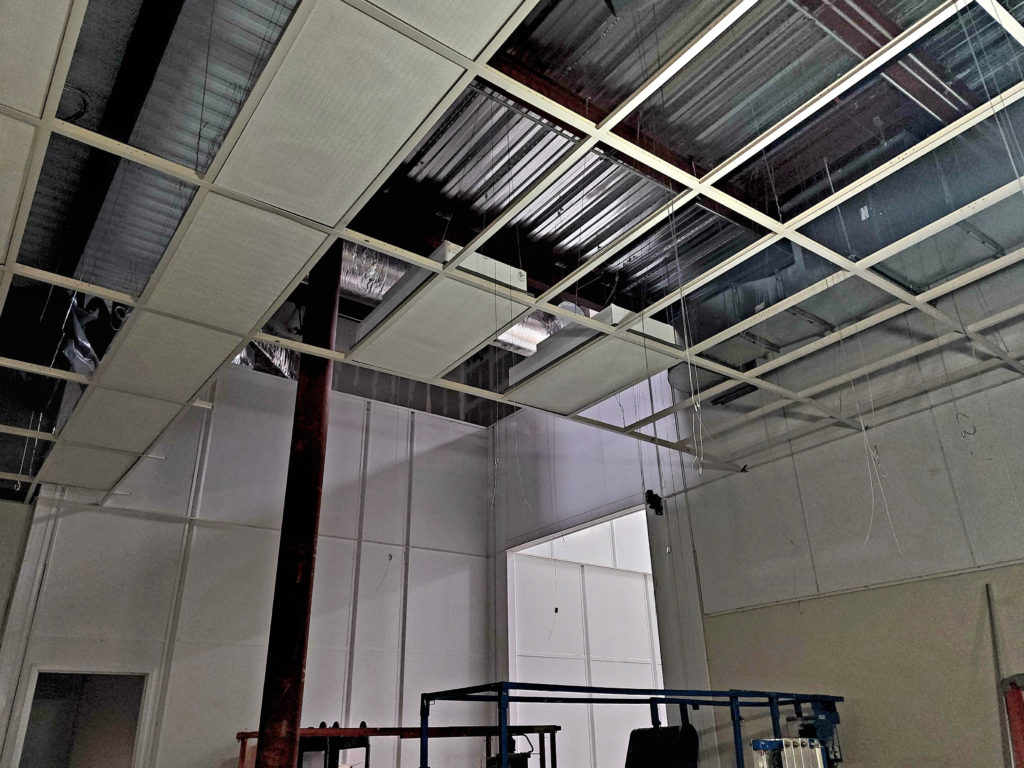
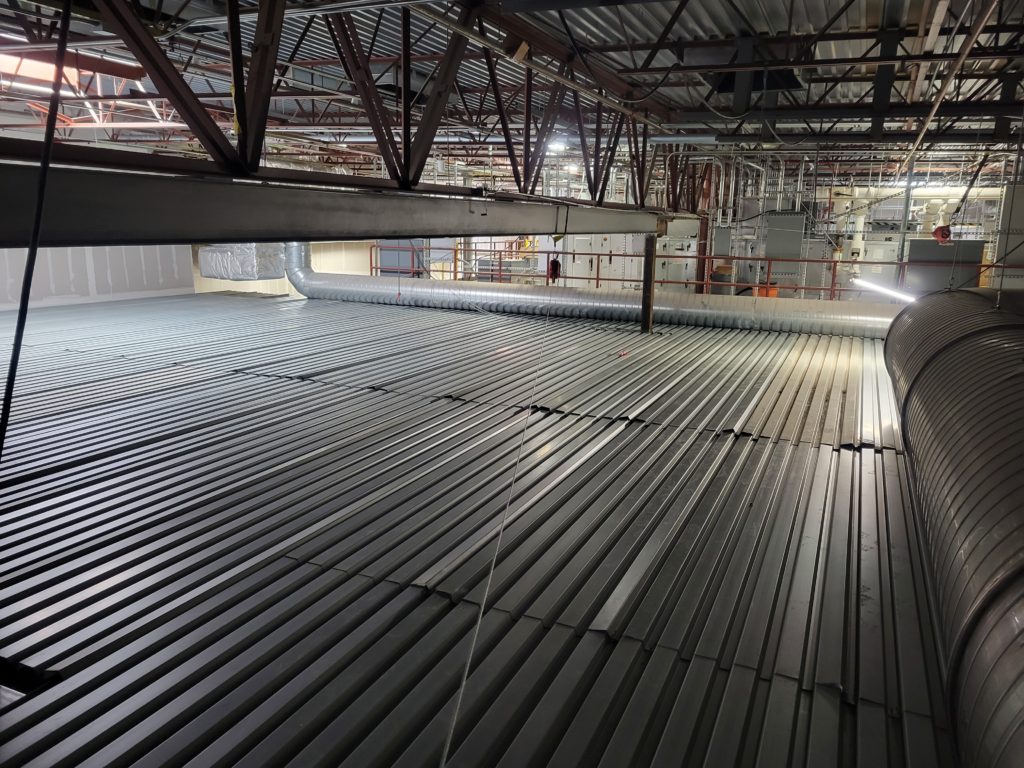
Raised Floors
In semiconductor cleanrooms, the flooring is not just underfoot; it’s a strategic component designed to enhance cleanliness and facilitate optimal air distribution. In this project, PAC elevated the cleanroom flooring three feet off the facility floor, creating unilateral airflow. This design enhances the cleanliness of the room by allowing for controlled air circulation, mitigating the risk of contaminants.
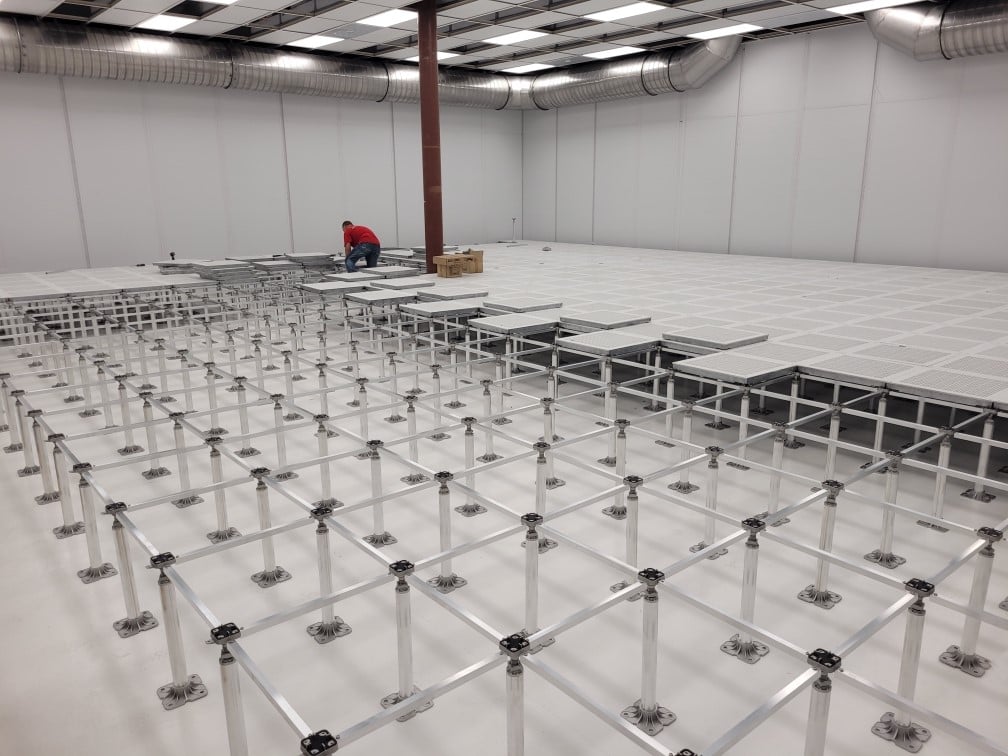
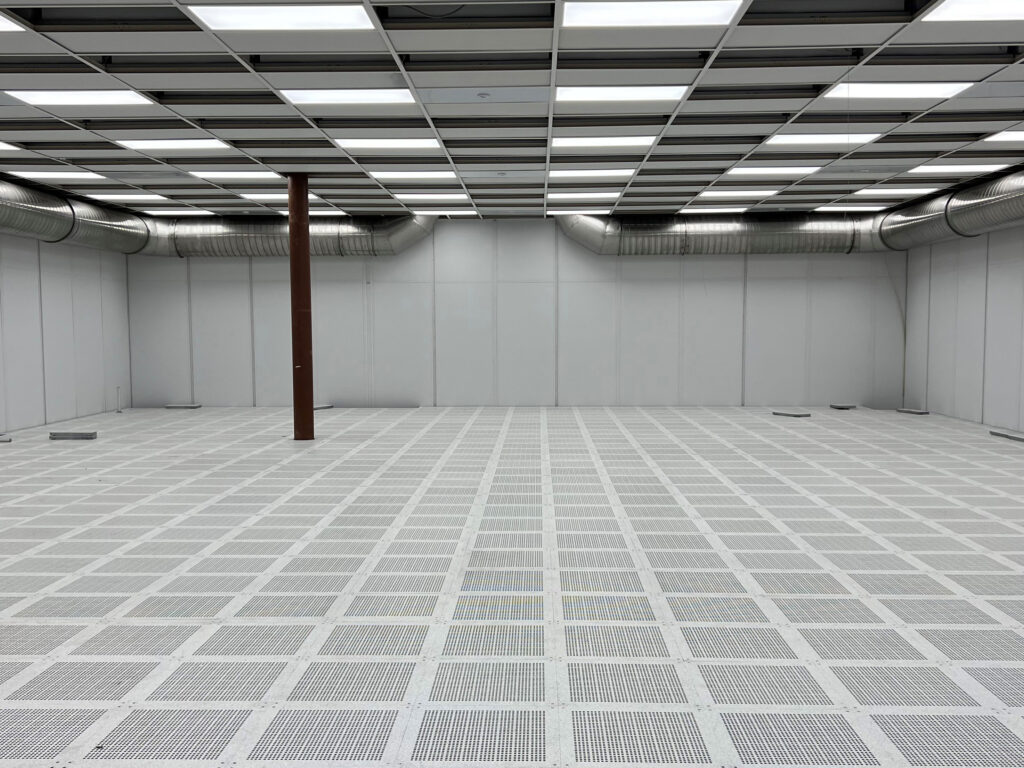
Air Flow System, HVAC, and Compressors: Breathing Life into Precision
The lungs of any cleanroom lie in its airflow system. The cleanroom expansion used a closed-loop, also known as recirculation, airflow system. Four HVACs and compressors, integrated with a walkable ceiling deck, catwalk, and mezzanine for accessibility, formed the robust infrastructure. An air chase, acting as the lungs of the cleanroom, ensured rapid and efficient air circulation every 15 seconds. Engineered ducts further optimized the air distribution, meeting the stringent requirements of semiconductor processes.
A reliable air conditioning structure ensures a controlled temperature environment, critical for the success of semiconductor equipment. With this cleanroom being located in the Arizona desert, the efficiency and effectiveness of the chosen air conditioning units were even more crucial. PAC’s conscientious approach to HVAC and compressors, combined with safety features such as catwalks and safety railings, guarantees both long-term functionality and personnel well-being within the cleanroom.
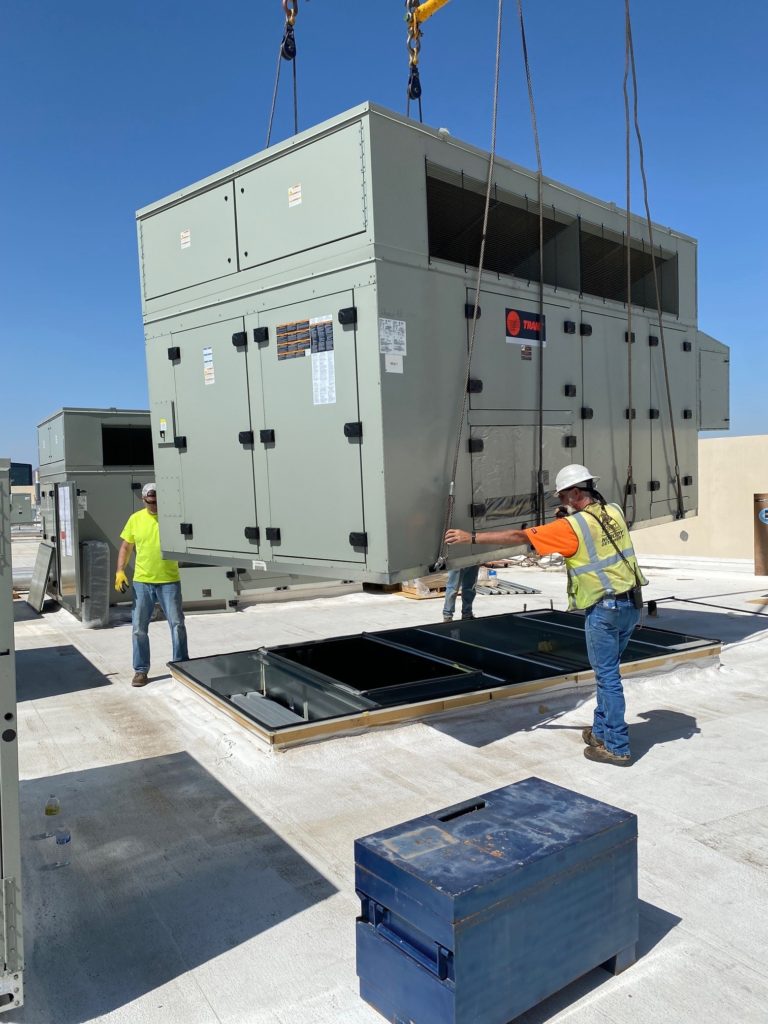
The Outcome
PAC’s role in this cleanroom expansion extended beyond construction. Our team, acting as the orchestrator of cleanroom resources, ensured a harmonious interplay of design, construction, and functionality. This project stands as a testament to our commitment to precision, cleanliness, and the relentless pursuit of excellence in semiconductor cleanroom construction.
Upgrading or Building a New Cleanroom?
CleanPro®, a division of Production Automation, is a trusted ally of enterprises, research facilities, and government agencies. We leverage 100 years of cleanroom experience to draft, design, schedule, and deliver production ready cleanrooms.
Related Posts
-
Cleanroom Construction FAQ
Definitive Cleanroom Construction FAQ: How much does a cleanroom cost? How does the level of ISO classification impact build and operating costs? How much supporting space will I need for a cleanroom addition or ISO…
-
CleanPro® Chemotherapy & CSP Cleanroom Installation
This modular, sterile compounding cleanroom is designed for USP 797 and USP 800 compliance, particularly for compounding chemotherapy drugs. Safe handling of sterile compounds requires special considerations: heat-welded floors, anterooms and buffer areas.
-
Cleanroom Installation Examples by CleanPro®
Here are some best-in-class cleanroom projects, in which the PAC cleanroom division, CleanPro, provided expertise and turnkey execution for design and installation of cleanroom enclosures, furniture, and components.
-
CleanPro® Cleanroom Installation
Cleanroom Wall System Installation Cleanroom Ceiling System Installation Completed Cleanroom & HVAC Installation Need Help with a Production Ready Cleanroom? PAC cleanroom specialists help you identify which components best suit for your application with respect…
-
CleanPro® Softwall Cleanroom Curtains Installation
Softwall cleanroom curtains, sometimes referred simply as “plastic strips” yield ISO Class 10,000 level particle control with minimal construction. This customer required a custom softwall installation that integrated into their existing building structure CleanPro to…
-
CleanPro® Softwall Cleanroom Enclosure
This customer needed to enclose a piece of machinery, and CleanPro® was able to provide a solution.