Table of Contents
Deaths of Medicinal Cannabis Patients Linked to Contaminants
Fingerprints of a Killer
A 2017 UC Davis study discovered multiple bacterial and fungal pathogens within California medical marijuana products.
The study was conducted after doctors identified a relatively rare but lethal fungal infection in two cancer patients who later died. They were relatively young, in winnable cancer battles.
In a subsequent study, the team gathered 20 samples of medical marijuana from across California and analyzed the samples for dangerous bacteria and fungi with DNA analysis.
"The cannabis was contaminated with many bacteria and fungi, some of which was compatible with the infections that I saw in my patients — Klebsiella, E.coli, Pseudomonas, Acinetobacter, these are all very serious infections for anybody in the hospital. But particularly in that population, the cancer population”.
“We were a little bit startled that ninety percent of those samples had something on them. These weren’t just any pathogens, [we] were looking at the very fingerprints of a killer.“
The connection of fungal infection to moldy marijuana isn’t a recently discovered phenomena. A 1981 study by the Milwaukee County General Hospital found evidence of fungus in the blood of 11 out of 12 marijuana smokers.
"The researcher also found antibodies produced by the body to combat the fungus in the blood stream of more than half of his subjects."
Infection Risk when Vaporizing or Smoking Tobacco and Marijuana
The threat of fungal infection is historically deadly, especially when introduced directly into respiratory or nervous systems.
Studies have shown that tobacco and marijuana harvests may yield significant amounts of fungal spores and plant pathogens such as Aspergillus. Aspergillus is associated with serious diseases in humans and animals.
Acute invasive aspergillosis is a form that grows into body tissue and is most common in those with weakened immune systems such as chemotherapy or AIDS patients. It is also known as a cause for neonatal infections.
- Invasive aspergillosis has been described in association with marijuana smoking in two cancer patients on chemotherapy, two leukemia patients, a renal transplant recipient, and a few patients with AIDS.
- There have been two reported cases of ABPA associated with moldy marijuana. Given the frequency of asthma and ABPA, and the high frequency of marijuana usage amongst young people, these cases may represent a tiny proportion of those affected.
For medical marijuana patients, direct exposure to vaporized cannabis products fuels complications and may accelerate, or even cause respiratory related ailments.
Once considered a weak pathogen, modern immunosuppressive therapies increase the likeliness of deadly infections amongst Aspergillus exposure.
A study conducted between 2008 – 2011 of patients with invasive aspergillus (IA) highlights a compelling mortality rate when a patient also sufferers from an underlying disease or immunodeficiency.
Of the 152 patients studied:
- Invasive Aspergillus infection played a role in 62 patient deaths (67.4%).
- In 36 cases, Invasive Aspergillosis a direct cause of death.
- Fifteen of those cases were diagnosed post-mortem.
The study indicates that IA infections are not only difficult to treat, but also difficult to detect. A preventative solution is essential.
Impact of Airborne Fungal Spores and Toxins on Cannabis Workers
Airborne fungal spores and toxins are also a concern for medical cannabis workers and processors. These CDC findings stir concern for the long-term health of cannabis cultivation workers exposed to fungal and bacterial strains known to cause harm against humans.
Another study from the organization National Jewish Health ads that molds also generate hazards specifically for indoor grow workers.
“The combination of warm temperatures and high humidity found in many indoor marijuana grow operations can fuel extensive mold growth....Airborne levels of mold spores that we found inside these structures may subject the occupants, emergency personnel and other individuals to significant health hazards, especially allergies, asthma, hypersensitivity, pneumonitis and other respiratory diseases."
- National Jewish Health Organization
Eliminating harmful pesticides and mitigating mold and fungus are crucial barriers for the success of medicinal cannabis products. Adoption of cleanroom technology proves historically advantageous in processing and production within biomedical, electronics, and pharmaceutical fields.
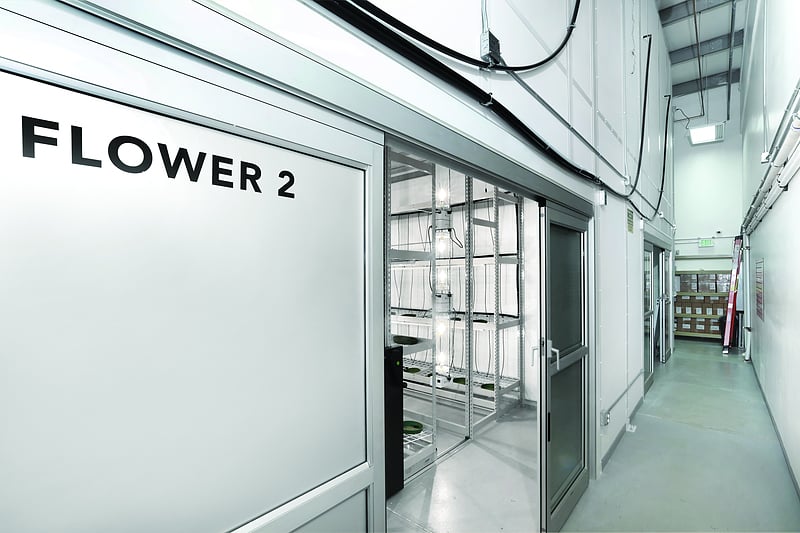
Advantages of Indoor Medicinal Cannabis Production
Large-scale cultivation of medical marijuana presents a number of challenges for potency and consistency. Differing cannabis strains, vegetative cycles, and cannabis production areas all require unique controls. The rigors of medicinal product approval and testing justify driving facilities out of dirty warehouses and into medical-grade environments.
Heavy pesticides and the presence of mold, mites, and microbes are primary barriers-to-scale for cannabis-derived medicine. Before we address the downsides and challenges of indoor grow rooms, we’ll first mention some of its historic advantages.
The Advantages of Indoor Medical Cannabis Grows
For photosynthetic processes controlling the intensity of light, temperature, and C02 is a cornerstone of translating gas and water vapor exchange into growth. Soilless indoor cannabis farming offers many benefits over traditional, outdoor farms: higher crop densities and yields, many more harvests per year, offer complete control over growing variables, and reduce pest and disease vectors.
Due to the allogamous (cross-fertilization) nature of the species, maintaining chemical profiles of THC product genotypes is difficult under outdoor field conditions. Indoor medical marijuana grows limit deviation, cross-pollination, improve security, regulatory control, and improve the quality and consistency of yields. In parallel, changes in global and seasonal weather patterns do not threaten the viability of climate-dependent medicines.
Challenges for Uncontrolled Indoor Cannabis Grows
Indoor grows face distinct challenges that outdoor grows do not. A tropical combination of heat, humidity, and moisture accelerate cannabis production, but also incubate bacteria, insects, and fungal families. The largest liability for cannabis producers is safety and the monetary risks of large-scale product contamination. Likewise, dosage accuracy and potency remains a challenge that the medical cannabis industry struggles to reach.
How Cannabis Grow Rooms Mitigate Fungus & Microbes
Canadian Medical Marijuana Regulation and Testing
In Canada, medical marijuana grows have staunch regulation, testing, and inspection.
Federal inspectors tour facilities monthly to ensure that cannabis grows meet national standards.
Contamination is core of concern. Sample testing is carried out by federally regulated laboratories, therefore the standard of expectations and results are more uniform.
Emblem Cannabis is one Canada’s largest medical marijuana cultivators.
"In order to grow a product capable of passing microbial tests, Emblem protects each grow room with positive air pressure. While typical hinged doors allow foreign particles to enter each time they’re opened, Emblem’s high-pressure rooms prevent contaminants from entering. Employees working inside the grow rooms cover themselves from head to toe in cleanroom suits to prevent anything on their clothing from contaminating the sealed environment. There’s not a lot of possibility for contamination between the grow rooms and in the processing areas; they are both separate, and a high degree of sanitation is required."
- Cannabis Business Times
Agricultural, supplement and pharmaceutical manufacturers face stringent regulation and accountability for the safety of patients and consumers. As state laws expand over medical marijuana manufacturing, testing, and labeling, cannabis cleanrooms offer medical marijuana growers a higher degree of certainty for meeting and exceeding regulatory standards.
US and State Regulations for Medical Marijuana Testing
In the USA, product testing is limited to state governed laboratories and protocols. Many states have adopted aggressive protocols for microbial testing.
In Connecticut, if a sample fails any microbial test based on the testing regulations set forth by the state, the producer must dispose of the entire batch without any sales or production.
In Colorado, new rules require testing for microbes (E. coli, salmonella and total yeast and mold) for flower, infused products and concentrates. Also, solvent-based medical marijuana concentrates must be tested for residual solvents.
California regulation includes microbiological impurity, including total aerobic microbial count, total yeast mold count, P. aeruginosa, aspergillus spp., s. aureus, aflatoxin B1, B2, G1, or G2, or ochratoxin A at levels that are lesser of either the most current version of the American Herbal Pharmacopoeia monograph or the State Department of Public Health.
The full cost of a contaminated product from seed-to-sale is a fraction of the cost when discovered before distribution: once it reaches markets, recalling a product is catastrophic. History has shown that poor manufacturing controls and shortcuts lead to undetectable risk and crippling penalties: emissions falsification, exploding phones, contaminated peanut butter.
How Does a Cannabis Cleanroom Improve Air Quality?
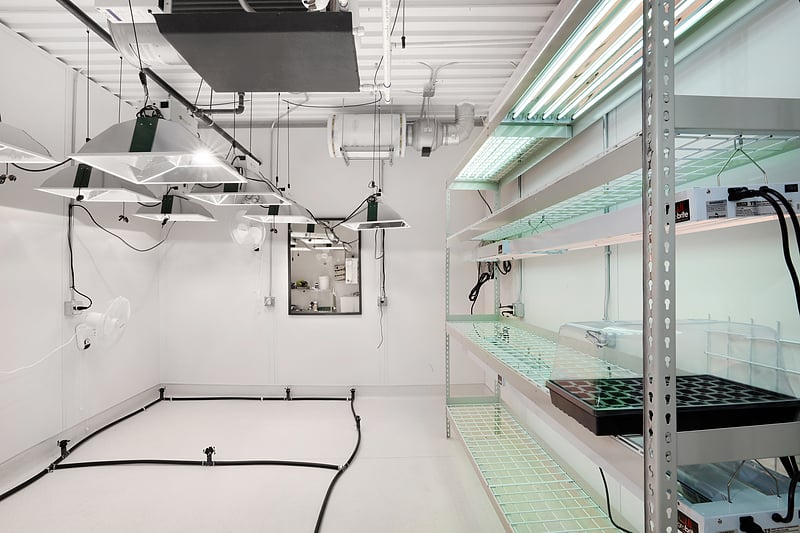
Generally speaking a “Clean Room” is an enclosed room that has equipment which controls the amount of particulate matter in the air by using air pressure and filters. To meet requirements of a “Clean Room” as defined by Federal Standard 209E and newer ISO Standards, all cleanrooms must not exceed a particulate count as specified in the air cleanliness class.
ISO 14644-1 Cleanroom Standards
Cleanrooms feature standardized class ratings that indicate the number of particles for each square meter or sq. ft. of air. An ISO Class 3 cleanroom is one of the cleanest human-occupied environments required for today’s technology. The pictured chart identifies the allowable particles sizes and the number of particles per each classification.
While higher levels of cleanliness are achievable, they are generally not required. Hypothetically cannabis cleanrooms could range from an ISO Class 5 as used in pharmaceutical cleanrooms, or upwards to an ISO Class 8 common for packaging and processing operations. Once the room is completed, most specifications call for testing and certification. Testing is usually conducted by an independent testing agency using the ISO Standards. It is also imperative for the owner to purchase a clean room monitor in order to determine the daily status of the room.
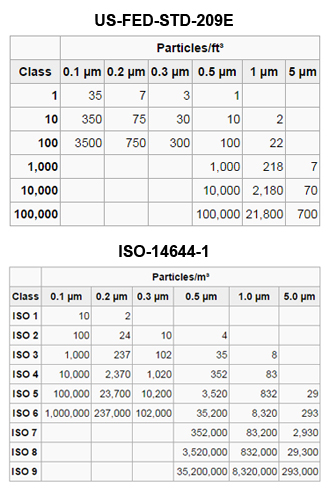
Controlling Temperature, Humidity, and Moisture for Medical Cannabis Grow Rooms
Bright, warm vegetation areas with plentiful water supplies harbor a number of unwanted bacteria and fungus.
Humidity levels that rise above 80% increase the risk of fungal, bacterial, and viral infections. Humidity levels that drop below 70% reduce photosynthetic efficiency and may affect yields. Much like a petri dish, bacteria or fungus incubates and may not be present immediately, but without environmental controls, the product is likely to fail bacteriological screening.
Water sprayed leaves create warm, wet environments that foster microbes, mildew, yeast, and fungus growth. The effect is accelerated when an unfavorable level of water vapor pressure generates dew condensation. The single most effective way to stifle the growth of mold and mildew is by controlling moisture, humidity, and temperature proactively.
Ideal Moisture & Humidity for Medical Marijuana Grows
The Cannabis Business Times offers an in-depth look at what cultivators must understand about the science of humidity to keep plants healthy and thriving.
Mark June-Wells, a laboratory director for Connecticut Pharmaceutical Solutions (CPS), is one of four licensed medical cannabis producers in the state. Dr. June-Wells holds a Ph.D. in botany/plant ecology from Rutgers University and has engineered CPS’ cannabinoid extraction efficiency and tracking programs. He developed one of the largest production databases in the United States and created efficient and repeatable production methods informed by rigorous data collection and statistical model building.
He states that a grow room should maintain a temperature between 75 ºF and 80ºF (18-26ºC) during light phases, and slightly cooler during dark phases (~70ºF.) Humidity levels vary within growing stages:
- Cloning: 70%-75% RH
- Vegetation: 65%-70% RH
- Flower: 60%-65% RH
- Night phase of flower: 55%-60% RH
How Cannabis Cleanrooms Improve Control of Moisture, Temperature, and Humidity for Medical Cannabis Grows
Because humidity and temperature maintain a direct relation, changes in temperature reflect in humidity levels and vice versa. Cleanrooms aid control of temperature and humidity swings by recirculating up to 80% of room air. Preconditioned air, once filtered and recirculated offers a higher degree of control and efficiency than once through systems that pull in 100% new air.
Preventing Powdery Mildew
Commercial cannabis grow rooms prevent powdery mildew (PM) with tight vapor pressure gradients, air flow, and humidity control. Well engineered airflow systems with HEPA filtration avoid recirculating airborne pathogens and fungal spores. Laminar flows minimize the congregation of dirty air, smooth thermal gradients, and regulate humidity variation during air changes. The result is a stabilized pressure that moves air methodically through a canopy. Evaporation and temperature variation is more methodical, therefore pressure variance is less pronounced and more controlled. Oscillating fans spread contamination throughout a space, therefore sacrificing cleanliness. Laminar airflow is filtered and recirculated with precision, thus contamination is avoided before a pesticide application is required.
Need help configuring your drying room based on product weight and square footage? We’ll help you customize your hemp or cannabis drying process to get the most amount of output without worrying about buds clumping, sticking, or flattening. Growers are able to harvest and dry cannabis with much smaller footprints, better throughput, and don’t worry about mold or flattening caused by solid trays.
Optimizing Vapor Pressure Deficit Improves Cleanliness for Cannabis Cultivation
""By creating a vapor pressure deficit [VPD, the difference between the amount of moisture in the air and what the air can hold at that temperature] in the flowering bays of our 2-acre greenhouse with our … automated environmental control system, Strawberry Fields has been able to prevent the growth of powdery mildew and Botrytis on over 25,000 lbs. of cultivated marijuana and has passed roughly 200 microbial tests, making it safe for consumption and available for wholesale..
- Samuel Thoman, Chief of Business Development for Strawberry Fields in Colorado
Cannabis Grow Room Wall Panels and Construction Features
Advancements in cleanroom wall panels unhinge control over not only exterior room dimensions and environments, but also over the properties of internal wall designs. Modular wall panels extend design freedom by offering customization of internal insulation for improved heat retention. The ability to integrate electrical conduits, product pass-throughs, windows, ducting, air filters, and storage cabinets into structural design accelerates installation and overall performance. Space and workflow are optimized on an application-specific basis. The rooms have very high insulation value which improves cooling efficiency, and they are tightly sealed which improves humidity control and prevents cross contamination.
The benefit of Modular Designs for Cannabis Grows
The benefit of modular cannabis cleanrooms over traditionally fixed wall grow rooms is that the configurable partitions of modular cleanroom designs lower the cost of installation or re-configuration for changing regulations. Divider rooms total environmental control, larger yields, and improve regulatory compliance at various stages of the growing cycle. Likewise, variable control and adjustment of humidity, temperature, and contaminants within each cell is a paramount advantage for consistency and potency over facilities with an uninterrupted passage between each staging room of a cannabis grow.
Assessing the Current Landscape and Trajectory of Medical Marijuana Regulation
The Importance of Controlled Grows for Medical Marijuana Products: Garnishing Pharmaceutical Caliber Results
The FDA’s (Food and Drug Administration) repackaged stance on medical marijuana drives new medical trials that will eventually define the future of medical marijuana grows. Tech-forward organizations find that controlled cannabis environments increase the quality and quantity of their product. A dynamic and adaptable system future proofs their operation for oncoming regulation. One could infer that the FDA’s 2018 consumer safety guidelines foreshadow the path of manufacturing, testing, and packaging for medical cannabis products.
- Consumers should consider requesting information on any pesticides, fungicides, fertilizers, or any other residual solvents that could remain on flowers after the cultivation process.
- Consumers should be sure to inquire about the potency and dosage of an edible product, especially if they are a novice consumer or if the package is not clearly labeled.
- Safety and quality require testing for mold, fungus, bacteria, and other microbial organisms. The effects of consuming some of these chemicals, especially in the immunocompromised, could be significant.
- Flowers and other cannabis products sold to consumers should include cannabinoid profiles on labels, including the content of THC, CBD and other major cannabinoids, and the number and concentration of doses. This is especially important for edible products, which can contain widely varying doses of cannabis.
A Cleaner Future for Medical Marijuana Cultivation
Medical marijuana cultivators understand that control over environmental, genetic, and nutrient variables are an undisputed production advantage for photosynthetic plants. Like all cleanroom applications, the cost-benefit analysis is a key requirement for understanding the need for a cleanroom facility. A cleaner future highlights that the potential of losing not just a marijuana plant, but an entire crop, or even a human life, is a core motivation in adopting new technology.
Learn More - Cannabis Grow Room Construction and Design
Want More Info on an Ultra-Clean Grow Room for Your Facility?
Production Automation (that’s us), and our CleanPro® cleanroom division offer critical class grow room construction, installation, and outfitting services. Our modular structures provide temperature control, controlled access, and contamination free entry with prefabricated walls and integrated conduits.
Related Posts
-
4 Ways to Maintain a Clean Grow Room
Grows rooms often provide a safe harbor for invasive insects, molds, fungus, and microbial pathogens. While one option is building a hyper-clean cannabis cultivation room, below we provide more economical production solutions which dramatically reduce…
-
Cannabis Drying Racks and Secure Storage
When it comes to cannabis drying racks, open-wire shelving designs have some advantages for processing and harvesting. Hanging, drying, and storing benefit from easy access with a steady flow of air that maintains temperature and humidity.…
-
Cleanrooms for Medical Cannabis Grows - Deaths Linked to Contamination
The benefit of modular cannabis cleanrooms over traditionally fixed wall grow rooms is that the configurable partitions of modular cleanroom designs lower the cost of installation or re-configuration for changing regulations. Divider rooms total environmental…
-
Sealed & Portable Medicinal Cannabis Grow Rooms
Modular cannabis grow room designs improve the longevity of grow room construction. Likewise, portable prefab grow rooms allow for more adaptable configurations when expanding, relocating, or re-purposing a grow room. There are also a number…
-
Why Every Cannabis Grow Room Design Should Incorporate an Air Shower
Most cannabis facilities prefer over-sized air showers, as transport carts and pallet jacks are often required at the beginning and end of grow cycles. Extra large air locks and pass-through air showers allow the passage…