How Do I Choose the Right Tool?
Choosing the right cutting tool requires an assessment of the task at hand, technician preference, economic justification, and ergonomics. The most capable cutter for the job will have the proper design features that best fit your application, such as material composition, handle properties, head/tip size, bevel, and edge sharpness.
Which Cutter is the Industry Standard?
Carbide, short for tungsten carbide, contains equal parts of tungsten and carbon atoms. It was developed by General Electric in 1925 and is approximately two times stiffer and two times denser than steel. Cutting hardened material repeatedly and accurately requires high durability. Device manufacturers use carbide-cutting tools because their working life is 20 times longer than traditional tooling materials. Its extreme hardness and heat resistance expand with heat induction and tempering providing distinct advantages in manufacturing applications. Carbide tooling resists abrasion and withstands much higher temperatures than steel counterparts.
Are Traditional Steel Tools a Thing of the Past?
Steel tools find favor over carbide when each person on the manufacturing floor requires a hand cutter, but only for general cutting tasks which do not warrant the premium cost of carbide tooling. Further, carbide cutters require diligent use. They can also become stiff and crack when pressure or cross-lateral force is applied to open a cutter with a stiff joint. Rapid heat cycles or improper sharpening followed by a stress load or improper usage can result in softened edges, degraded cutting properties, and sometimes damage beyond repair. Steel provides an economic solution and easy replacement with minimal need for maintenance. Most carbide tool manufacturers carry lifetime product warranties, but when tools are misused these warranties may not be honored.
What are the Grip Characteristics of Manufacturing Hand Cutting Tools?
Touch, feedback, comfort, and dexterity are traits that make tools effective in the field. Manufacturers develop tools with various shapes, grip construction, handle width, and handle length for production needs and user preferences. Traditional “C” shaped handles aid free movement and visibility, and enable quick arm movement. Ergonomic dual curve cutters expand production capability by reducing fatigue. This helps technicians focus on precision and output with maximized comfort. Short handles and snug fit of the palm maximize the free use of fingers for placement and movement of the component receiving service. Long handles provide the most cutting power and help dissipate cutting shock more evenly. Sometimes, the sole factor in determining the optimal shape and handle size is operator preference.
Alternatively, some environments require tool features for safely handling products during rework or assembly. PCB and electronics manufacturers require ESD-safe cutting tools which dissipate static discharge and limit the risks of destroying sensitive electronics. High-volume facilities with large inputs of manual labor invest in the most suitable grips and cutter whether it requires rapid shearing or versatile cuts. Comfortable, soft grips reduce the risks associated with developing carpal tunnel syndrome for technicians.
Adjustment points in the cutting head pivot and adjustable leaf springs further enable smooth pressure delivery for reduced shock and easy cutting. Preset tool adjustments shorten cutting action, quicken cuts, and reduce overall exertion and fatigue. The cost structure of cutting tools rises with additional features because of more specialized construction. Regardless, these features find worthwhile production boosts in production use.
Do Flush Cut Designs Find Favor in Medical and Electronics Manufacturing?
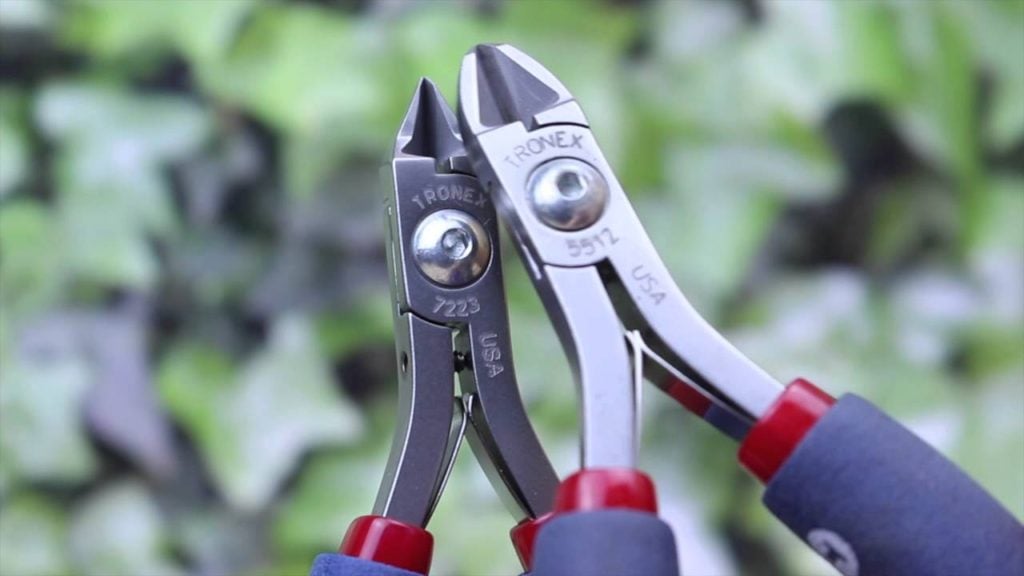
The most common type of hand cutter in medical and electronics manufacturing is the flush cut design. In commercial use, this cutter receives praise for overcoming materials like piano wire, tungsten, platinum, most stainless steel including MP35N-V, and even Nitinol with a spikeless, fine finish. Selecting the proper cutting type facilitates repeatable cuts with minimal energy transfer and repeatable results.
Semi-flush edge design, or beveled, is the most durable and longest-lasting of flush designs. It does, however, require the most grip pressure. More aggressive angled cutters, such as flush, require less grip pressure and yield the cleanest cuts. Producing delicate devices requires flush cutters because the shock and impact of the cutting process can damage sensitive components. Adversely, they also dull more quickly and require servicing or replacement in shorter cycles.
How Can I Determine the Proper Head/Tip Type?
The terms ‘head’ and ‘tip’ are often used interchangeably. Both refer to the cutting head’s shape, circumference, thickness, and geometries. Peak productivity and the best cost per cut require specialized tooling and sometimes custom order honing and engineering for perfect fit and function. Manufacturers of the world’s smallest components rely on cutters with uniquely designed heads and tips for work within closely spaced components. The four most commonly used head shapes are oval, oval slim, tapered, and slim tapered. Oval head cutters offer the longest life span and are the most durable of all cutting heads. Wide jaws and a thick cross point ensure a contact point with a strength that is more resistant to dulling but also requires higher grip pressure. Slim designs provide an intermediate functionality of ease of cutting, accessibility, and durability. Micro tips provide ultimate access to tight spaces and increase breakage due to smaller cross-sections near the tip.
Hand Tools Are Not One-Size-Fit-All
Determining how to choose the proper cutter requires assessing the economic and production floor value on a case-by-case basis. The variables of workflow, application, material use, and requirements by specific industries don’t cater to one-size-fits-all features.
Take a moment to browse offerings from multiple manufacturers and get familiar with standard and specialized features. If in doubt, contact a PAC product expert for help discovering your ideal production tool.
Related Posts
-
New Accuform Manufacturing Signage
Are you in compliance? Do you qualify for an exemption? Generic signage no longer adheres to recent Proposition 65 updates. Custom order Accuform signage is now available from PAC. Our specialists tailor hazard signage for…
-
New: JOKARI Wire Strippers and Cutters
Modern technology requires modern tools. JOKARI‘s Original is a professional standard for stripping and dismantling wire or cable. Production Automation carries JOKARI wire and electrical tools because they enable both general production and specialized work.…
- Lean Cellular Manufacturing: Processing, Methods, Layouts, and Implementation
Cellular manufacturing helps reduce waste by reducing defects that result from processing and product changeovers. Since products or components move through a cell one piece at a time, operators can quickly identify and address defects.…
-
Finding a High Performance IC Socket Manufacturer
Overall size and method of attachment is crucial to ideal fit and function. Off-the-shelf solutions don’t always fit specific requirements for outdated or rare hardware. Custom designed IC sockets accommodate rare device configurations, odd sizes,…
-
Selecting the Best Workbench for Manufacturing, Electronics, Packaging, Or Assembly
This step-by-step guide will help you choose the right industrial workbench for all your needs. The best workbench buyers guide for information on best sizes, lighting, accessories and applications.
-
Mobile Hand Washing Stations and Sinks for Manufacturing
Portable hand sinks have internal water supply and waste water storage. The standalone unit with powered pump supply requires no additional plumbing, drains, or inlets.