The Electronics Manufacturing, Medical Device, Aerospace, and Defense Industries
The function of thermal interface materials is to fill the gaps between heat-generating components and heat sinks in different applications. In the electronics manufacturing, medical device, aerospace, and defense industries, thermal interface materials play an indispensable role in effectively managing thermal issues.
These industries face a number of challenges in terms of heat dissipation. Some of these challenges include:
- The miniaturization of electronic components, which has led to increased heat generation
- The close proximity of medical devices to the human body poses a risk of thermal injury and malfunctions if the devices overheat
- The extreme temperatures and vibrations that aerospace vehicles are subject to
- The harsh environments, such as high altitudes and extreme temperatures, that defense systems often operate in
To address these high-risk challenges, a reliable solution that can guarantee successful thermal management becomes imperative. The use of thermal interface materials not only prevents overheating, but also extends the lifespan of devices, and improves their overall performance.
Electronics Manufacturing
Heat Dissipation and the Red Ring of Death
Electronic devices generate heat as they operate. This heat must dissipate to prevent the devices from overheating and malfunctioning. In electronics manufacturing, heat dissipation can be a challenge because of the following factors:
- Smaller and more powerful devices. Electronic devices are becoming smaller and more powerful, meaning they generate more heat per unit volume. This makes it more difficult to dissipate heat effectively.
- Complex designs. Electronic devices often have complex designs with multiple heat sources. This can make it difficult to design an effective thermal management system.
- Limited space. Electronic components are often designed to fit into small spaces, such as laptops or smartphones. This limits the options for heat dissipation.
- Environmental factors. The operating environment can also affect heat dissipation. For example, devices that are used in hot or humid environments will need to be able to dissipate heat more effectively.
If heat dissipation is not done properly, it can lead to several problems, including device malfunction, reduced lifespan, and safety hazards. The Red Ring of Death (RROD) Xbox phenomenon of the early 2000s is a prime example of this challenge.
The Xbox 360 was designed with a low-profile case, which limited airflow. This made it difficult for the console to dissipate heat, especially when playing demanding games. Over time, dust could build up inside the console, further restricting airflow.
Additionally, the heat sinks used in the Xbox 360 were not effective at dissipating heat. In some cases, the thermal paste used to transfer heat from the CPU and GPU to the heat sinks was not applied correctly or degraded over time, contributing to heat buildup.
Overclocking the Xbox 360 could also cause the RROD. Overclocking is the process of running the console at a higher clock speed than it was designed for. This can improve performance, but it also generates more heat. The combination of these factors could cause the Xbox 360 to overheat. When the console overheated, it would shut down to protect itself from damage causing the red ring of death to appear on the console’s power ring.
Thermal Conductivity in Drone Assembly
Thermal conductivity is the measure of how well a material conducts heat. In electronics manufacturing, thermal conductivity is important because it determines how well heat can transfer away from heat-generating components, such as transistors and integrated circuits.
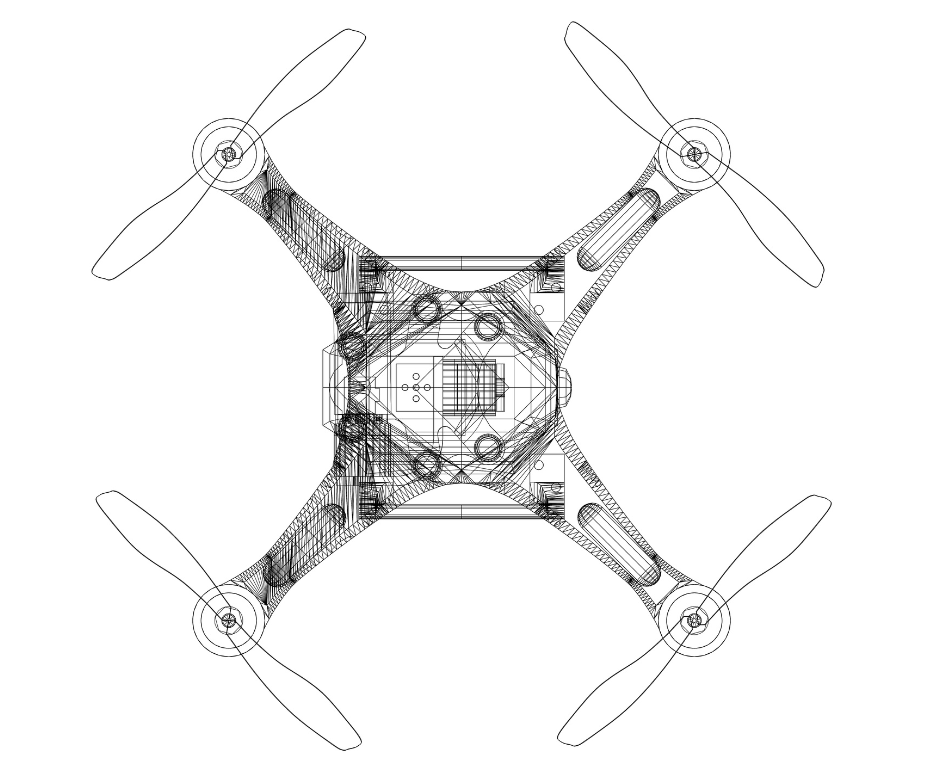
A good example of this challenge is drone assembly. Drones are complex electronic devices that generate a large amount of heat. This heat needs to dissipate efficiently to prevent the drone from overheating and failing. However, there are several challenges that electronics manufacturers face with thermal conductivity in drone assembly.
One challenge is that drones are typically minuscule and lightweight. This means there is minimal space for heat sinks and other cooling devices. Drones often operate in hot environments, which can make it difficult to dissipate heat.
Another challenge is that drones are often made up of a variety of different materials, each with its thermal conductivity. For example, the drone’s frame may be made of aluminum, while the battery may be made of lithium-ion. These different materials can create thermal interfaces, which can restrict heat transfer.
Finally, drones often have complex geometries, which can make it difficult to design and implement effective cooling solutions.
Contact Resistance in Chips
Contact resistance is an anomaly where heat flow is interrupted at the contact of two surfaces. It is a major factor in determining the performance of electronic devices, as it can lead to heat dissipation problems, power loss, and device failure.
In electronics manufacturing, contact resistance can be a challenge because of the following factors:
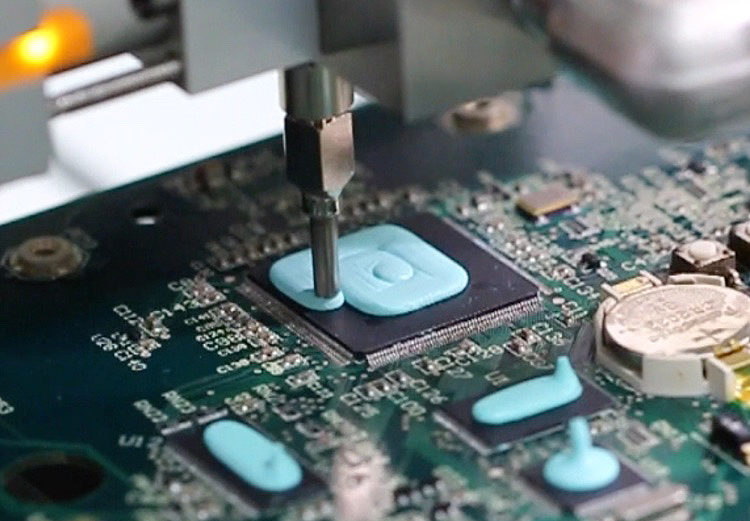
- Smaller and more complex devices. Electronic devices are becoming smaller and more complex, which means the contact areas between the different components are also becoming smaller. This can lead to higher contact resistance.
- Different materials. The different materials used in electronic devices can also contribute to contact resistance. For example, the contact resistance between copper and silicon is much higher than the contact resistance between copper and copper.
- Surface roughness. The surface roughness of the contacting surfaces can also affect contact resistance. A rougher surface will have more peaks and valleys, which can trap air and other contaminants, leading to higher contact resistance.
- Operating temperature. The operating temperature of the device can also affect contact resistance. As the temperature increases, the contact resistance typically decreases. This is because the temperature increase can help break down the air and other contaminants that are in a trap at the contact interface.
More specifically, in chips, contact resistance can occur at several different interfaces, including:
- Between the chip and the heat sink
- Between the chip and the substrate
- Between the transistors and the metal interconnects
Contact resistance can be particularly problematic in high-power chips, as it can lead to significant heat generation. This heat can cause the chip to overheat, which can lead to performance degradation and even failure.
Medical Device Manufacturing
Heat Dissipation in Pacemakers and Defibrillators
Pacemakers and defibrillators are medical devices that are implanted in the body to regulate the heart rate. These devices generate heat as they operate, and if the heat does not dissipate properly, it can damage the device or cause tissue damage.
The following factors contribute to the challenge of heat dissipation in pacemakers and defibrillators:
- Small size. Pacemakers and defibrillators are small devices with limited space available for heat dissipation.
- Active components. These devices contain active components, such as transistors and integrated circuits, which generate heat.
- Close proximity to the body. Pacemakers and defibrillators are implanted in the body making them close to the body’s heat.
Thermal Management of MRI Machines
Magnetic resonance imaging (MRI) machines create detailed images of the body by using a strong magnetic field and radio waves. These machines generate a lot of heat, which must dissipate properly to prevent damage to the machine or injury to the patient.
The factors that contribute to the challenge of thermal management in MRI machines are as follows:
- High power consumption. MRI machines consume a large amount of power, in turn generating lots of heat.
- Superconducting magnets. These machines use superconducting magnets, which require them to be cooled to low temperatures.
- Complex design. MRI machines are complex devices with multiple heat sources.
- Limited space. They are often in small spaces, which limits the options for heat dissipation.
Cooling of Surgical Lasers
Surgical lasers perform a variety of medical procedures, such as cutting, cauterizing, and welding. These lasers generate a large amount of heat, which must dissipate properly to prevent damage to the laser or injury to the patient.
Cooling surgical lasers poses a challenge due to the following factors:
- High power output. Surgical lasers typically have high-power outputs generating a lot of heat.
- Small size. Surgical lasers are often small devices, which limit the amount of space available for cooling.
- Close proximity to tissue: These lasers are often in close contact with tissue, making it possible for heat to transfer to the tissue and cause damage.
Thermal Management of Wearable Devices
The surge in the popularity of wearable devices stems from their unparalleled convenience in monitoring health data, yet it is vital to acknowledge their heat dissipation challenges.
The complexity of thermal management in wearable devices stems from the following factors:
- Small size. Wearable devices are often small, limiting the space available for heat dissipation.
- Close proximity to the body. Wearable devices are often close to the body, meaning the heat can transfer to the body and cause discomfort.
- Active components. Wearable devices often contain active components, such as sensors and processors, which generate heat.
Aerospace and Defense
Heat Dissipation in Avionics
Avionics systems are becoming increasingly complex and power-hungry, which is putting a strain on the ability to dissipate heat. This is a major challenge for avionics manufacturers, as heat can damage components and lead to system failure.
The following factors are responsible for the challenge of heat dissipation in avionics:
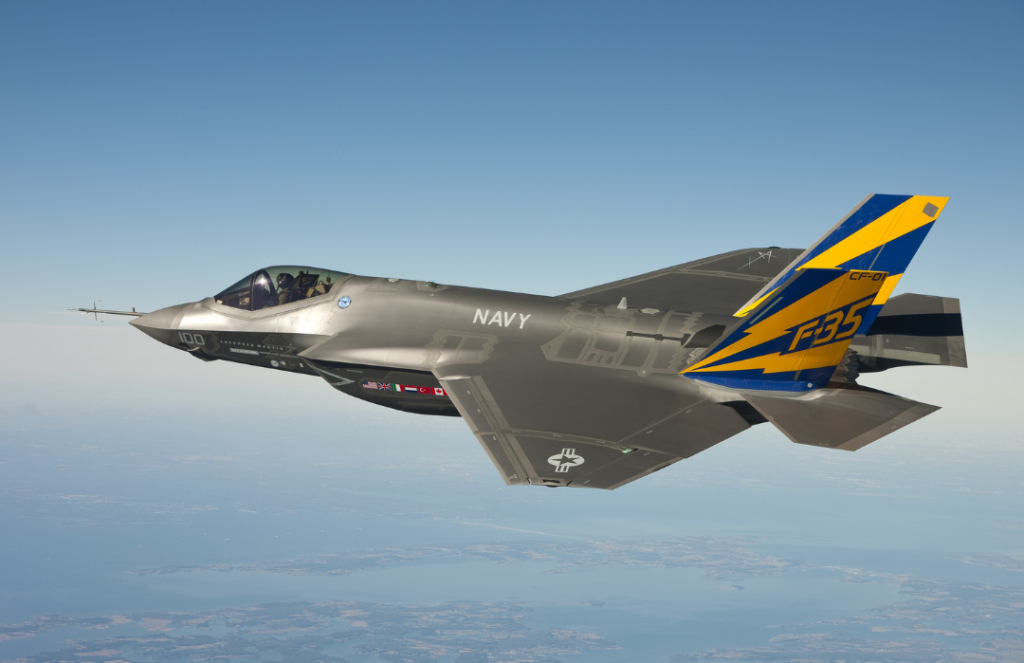
- The increasing power consumption of avionics systems. Avionics systems are becoming increasingly power-hungry, due to the use of more advanced components and features. This is putting a strain on the ability to dissipate heat.
- The limited space available for heat dissipation. Avionics systems are often in tight spaces, limiting the options for heat dissipation.
- The harsh environmental conditions. Avionics systems are often exposed to harsh environmental conditions, such as high temperatures and vibration, which can make it difficult to dissipate heat.
Thermal Management of Missiles and Rockets
Missiles and rockets are complex systems that generate a large amount of heat. This heat can come from the propulsion system, the electronics, and the materials used in the construction of the missile or rocket.
The challenge of thermal management in missiles and rockets is to ensure the heat dissipates efficiently and evenly so the system does not overheat and malfunction.
Several factors make thermal management in missiles and rockets challenging. These include:
- The small size and weight of missiles and rockets. This limits the amount of space available for heat sinks and other cooling devices.
- The propulsion system generates high temperatures. The combustion process in the propulsion system can generate temperatures of thousands of degrees Celsius.
- Missiles and rockets face harsh environmental conditions. These conditions can include high temperatures, vibration, and humidity.
Heat Transfer in Satellites
Satellites operate in a vacuum, which means there is no air to conduct heat away from the spacecraft. This makes heat transfer a critical issue for satellite design and operation.
The challenge of heat transfer in satellites is due to the following factors:
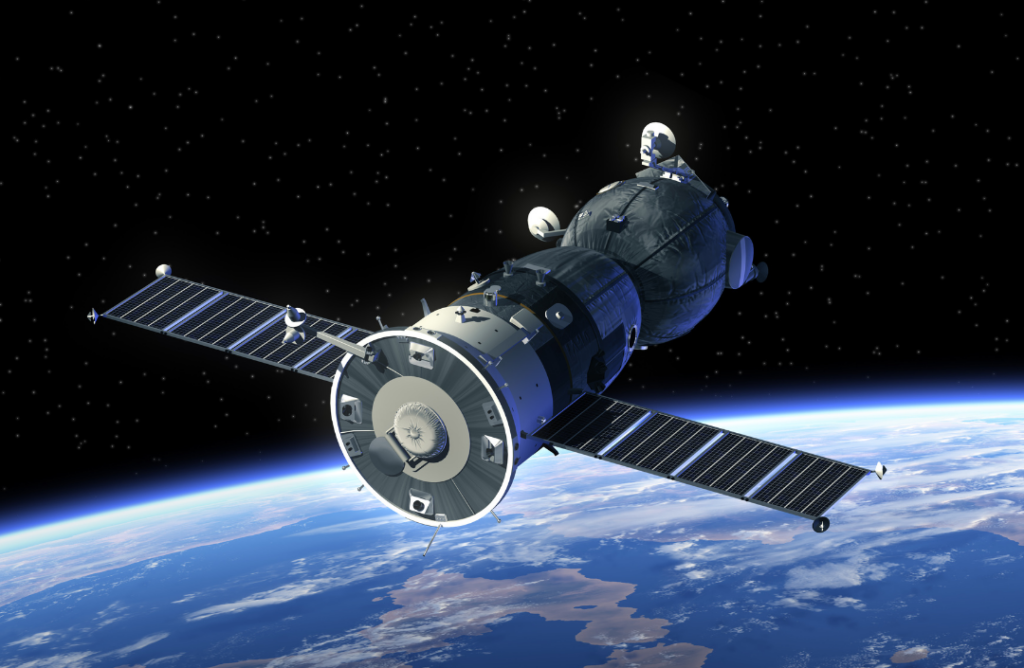
- Thermal radiation: The sun and other sources of heat in space emit thermal radiation. The satellite can absorb the radiation and heat it.
- Thermal conduction: Heat can also conduct through the materials that make up the satellite. This can happen through conduction between different parts of the satellite or conduction between the satellite and its surroundings.
- Convection: Convection is the transfer of heat through the movement of fluids. This can happen in satellites if there is a fluid present, such as a coolant.
Thermal Management of Unmanned Aerial Vehicles
Unmanned aerial vehicles (UAVs) are becoming increasingly popular for a variety of applications, such as surveillance, mapping, and delivery. However, UAVs also generate heat, which can be a challenge to manage.
The following factors give rise to the challenge of thermal management in UAVs:
- The small size of UAVs. UAVs are often small and lightweight, limiting the amount of space available for heat sinks and other cooling devices.
- The high power consumption of UAVs. UAVs often use powerful electronic components, which can generate a large amount of heat.
- UAVs are exposed to harsh environmental conditions. These conditions include high temperatures, vibration, and moisture, which can make it difficult to dissipate heat.
The Solution: Thermal Interface Materials
Many challenges in electronics manufacturing, medical device, aerospace, and defense industries are complex issues with no single solution that will work for all applications. Manufacturers can ensure safe and reliable product operation by understanding thermal conductivity challenges and using appropriate techniques.
Thermal interface materials are a great way to tackle many of the challenges faced in these industries. By filling in any gaps between the heat source and the heat sink, thermal conductivity can improve, allowing heat to transfer more efficiently. There are a variety of thermal interface materials available, each with its own advantages and disadvantages. PAC presents a premier line of thermal interface materials, contributing to the mitigation of these challenges. This line includes thermal gap pads and liquid gap fillers.
Thermal Gap Pads
Thermal gap pads are soft thermal interface materials that fill gaps between a heat source and a heat sink. They are typically made of a silicone or polymer material with high thermal conductivity. Thermal gap pads are used in a variety of applications, including electronic devices, automotive, medical, and aerospace.
Thermal gap pads have several benefits including:
- Better conformability. Thermal gap pads are more conformable, which means they can fill gaps and conform to irregular surfaces more easily.
- Less risk of air bubbles. Thermal gap pads are less likely to form air bubbles which are a major source of thermal resistance.
- Long-lasting. They can last longer because they are not as susceptible to drying out or squeezing out of the gap.
Liquid Gap Fillers
Liquid gap fillers are thermally conductive gap-filling materials used to enhance thermal transfer between an electronic component generating heat such as integrated circuits or transistors and a mechanical component carrying the heat to the exterior such as a heatsink. These fillers are dispensed in liquid form and then cured to form a solid, conformable material.
Here are some of the benefits of using liquid gap fillers:
- Easy application: Liquid gap fillers can be dispensed using a syringe or pump.
- Can fill larger gaps: They can fill gaps up to 0.5 mm wide.
- Optimal thermal performance: They have higher thermal conductivities than thermal paste.
- Compatible with a variety of materials: Liquid gap fillers can be used with a variety of materials, including metals, plastics, and ceramics.
PAC’s premier line of thermal interface materials will help mitigate heat dissipation, contact resistance, and thermal conductivity challenges in all of your operations.
Related Posts
-
Laird Thermal Interface Materials Now at PAC
The overheating of electronic components and systems remains a tough roadblock for electronics manufacturing, aerospace, semiconductor, and other relevant industries. When overheating occurs electronic components and systems experience premature failure and hindered performance and lifespans,…
- Steinel Heat Guns
Production Automation is excited to announce that we will now be offering Steinel Heat Guns! Steinel uses cutting edge technology to develop innovative solutions for today's world. High standards at every level of product design…
-
Mobile Hand Washing Stations and Sinks for Manufacturing
Portable hand sinks have internal water supply and waste water storage. The standalone unit with powered pump supply requires no additional plumbing, drains, or inlets.
- FLIR Thermal Imaging Cameras
A Thermography Hero's Welcome Patrol officers, security personnel, and American troops use FLIR infrared technology to protect lives and resources every day. In many ways, you as a thermographer do, too. With thermal imager in…
-
New Accuform Manufacturing Signage
Are you in compliance? Do you qualify for an exemption? Generic signage no longer adheres to recent Proposition 65 updates. Custom order Accuform signage is now available from PAC. Our specialists tailor hazard signage for…
-
GMP Cleanroom Design Standards Part 1: GMP and CGMP Manufacturing
What is GMP? What is CGMP? What are the differences between GMP and CGMP cleanrooms?