Advantages for Modular Hardwall Design and Construction of ISO 14644-4 Cleanrooms
Establishes a Controlled Environment: Hardwall cleanroom wall panels and components are engineered to provide a secure, controlled environment within the cleanroom.
Progressive Design: As needs change, modular cleanroom wall panel designs offer the ability to relocate or expand the cleanroom in the future.
Special Cleanroom Panel Sizes: Wall panels can be made in special sizes for entry areas, gowning rooms, and air-locks, ensuring that the cleanroom pressure remains constant. Extra-high, wall panel systems can accommodate large equipment which can require ceilings higher than the standard eight feet.
Load Considerations: Load-bearing cleanrooms require consideration of three factors for construction. The first factor is the amount of total weight on the cleanroom wall, the second factor is the span distance between all four of the cleanroom walls and the third factor is the height of your wall.
Once Through Design: Ambient air is drawn into the fan filter unit at the ceiling level. The filtered air passes into the cleanroom and is transferred out of the room through grilles at the bottom of the walls.
Recirculating Design: Recirculating cleanrooms are ideal when temperature or humidity control is required.
Elements of Modular Hardwall Cleanroom and Partition Construction
Cleanroom Wall Material: Prefab cleanroom wall panels find favor in quick turn cleanroom construction, but custom built modular wall panels continue to grow in popularity. Self-supporting walls increase design freedom for both large and small installations. Notably, fire and soundproof wall panels with polystyrene cores provide excellent thermal insulation and sound deadening properties.
T-Grid Ceiling System: Cleanroom T-grid systems support the integration of lighting, diffusers, tiles, and other integrated design features. These systems include all connectors, suspension hardware and gaskets which are then applied on site.
Ceiling Support Structure: Suspension support beams attach to the top of modular cleanroom walls for suspending a T-Grid Ceiling System. The sturdy structure removes the need for support from the host building.
Cleanroom Ceiling Tile Grid Systems and Panels: Ceiling panels with sealed edges for spaces provide particulate control in spaces not occupied by fan filter units or light fixtures.
Cleanroom Lighting: Cleanroom light fixtures are common in 2′ X 4′ configurations. 4-lamp cleanroom light fixtures with energy-efficient T8 electronic ballasts provide flicker-free startup and better overall efficiency. Cleanroom lights feature sealed housings and low profile, recessed construction for minimal particle retention and easy wipedown.
Cleanroom Pass-Thrus: Pass-thru cabinets allow you to move a product from one environment to another without affecting the cleanliness levels in your cleanroom.
Cleanroom HEPA Filters: Standardized cleanroom are commonly sized in 2′ x 4′ units with options for 115V (60 Hz), 208-230V (50/60 Hz), and 277V (60 Hz). 99.99% HEPA filtration is supported by variable speed control and all other standard specifications. The average cost of a HEPA filter unit for cleanroom specifications varies with cleanliness requirements and amount of air changes per hour. Getting a free quote is always an option.
Guidelines for selecting HEPA Filter Units (FFU): Sometimes getting help making the calculations necessary to achieve the desired ISO or U.S. Federal Standard 209 Class is essential. The correct quantity of HEPA or ULPA grade filters will be selected using air changes per hour as the most effective method for meeting class requirements.
Cleanroom Monitoring, Testing, and Validation Systems: Particle monitoring systems provide sophisticated computer-based monitoring systems for critical applications. They are ISO-9001/2008 certified, and the development processes meet cGMP standards. In addition to SCADA and general process control systems, there are over 200 systems installed in hospitals, clinics, and laboratories as well as pharmaceutical manufacturing operations throughout the world.
Cleanroom Validation and Classes
How Are Cleanroom Standards Determined?
The number and size of particles allowed in the room determine the classification of air cleanliness. See the ISO standards table for cleanroom classification requirements related to your application.
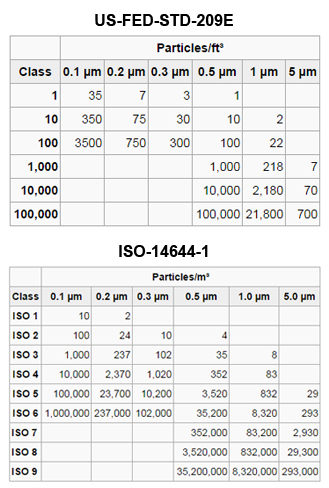
Finding A Prefabricated Cleanroom Manufacturer
Production Automation (that’s us) works with a network of authorized installers for complete cleanroom installation services, testing, and certification. Our engineers work closely with you to answer questions, define specifications, and provide affordable cleanroom manufacturing options for not only prefabricated cleanrooms, but also custom built solutions. Pre-engineered, modular design cleanrooms are cost-effective without the inconvenience of conventional “stick-built” construction, therefore, getting a quote is free and easy. Just fill out the web form, and select your ideal cleanroom configuration. As a broadline distributor and manufacturer’s representative of brands like CleanPro, Portafab, Terra Universal, and more, we enable faster turnaround via a network of warehouses, prefabricated cleanroom manufacturers, and suppliers across the United States, Canada, Mexico, and Central America.
Related Posts
-
CleanPro® Stand Alone Hardwall Cleanroom
CleanPro’s modular hardwall cleanroom solutions adapt alongside changing floor and production layouts.
-
Class 10,000 Cleanroom & Gowning Area
This cleanroom and adjacent gowning area helped this customer prevent outer contamination from entering classified spaces.
-
CleanPro® Softwall Cleanroom Enclosure
This customer needed to enclose a piece of machinery, and CleanPro® was able to provide a solution.
-
CleanPro® Turnkey Cleanroom Install
CleanPro’s turn-key cleanroom solution provided a one-stop, one-contact result for the initial delivery and on-site installation of walls, ceiling grids, electrical systems, flooring, filters, HVAC, and more.
-
Why is Modular Cleanroom Design A Huge Development?
Pre-engineered fabrication consolidates scheduling with minimal disruption and fewer variables. Difficult or expensive upgrades avoid overbearing noise, construction artifacts, and minimize if not eliminate the burden on facility staff for project management.
-
CleanPro® Stand Alone Hardwall Cleanroom
CleanPro’s modular hardwall cleanroom solutions adapt alongside changing floor and production layouts.